Adaptive inverse control system for chemical-mechanical polishing machine
A chemical-mechanical, self-adaptive inverse technology, applied to grinding automatic control devices, grinding machine parts, grinding/polishing equipment, etc., can solve problems such as pressure fluctuations in chemical-mechanical polishing CMP systems and reduced wafer polishing quality , to achieve the effect of reducing adverse effects, reducing system turbulence, and eliminating coupling
- Summary
- Abstract
- Description
- Claims
- Application Information
AI Technical Summary
Problems solved by technology
Method used
Image
Examples
Embodiment Construction
[0037] Embodiments of the present invention are described in detail below, examples of which are shown in the drawings, wherein the same or similar reference numerals designate the same or similar elements or elements having the same or similar functions throughout. The embodiments described below by referring to the figures are exemplary only for explaining the present invention and should not be construed as limiting the present invention.
[0038] These and other aspects of embodiments of the invention will become apparent with reference to the following description and drawings. In these descriptions and drawings, some specific implementations of the embodiments of the present invention are specifically disclosed to represent some ways of implementing the principles of the embodiments of the present invention, but it should be understood that the scope of the embodiments of the present invention is not limited by this limit. On the contrary, the embodiments of the present...
PUM
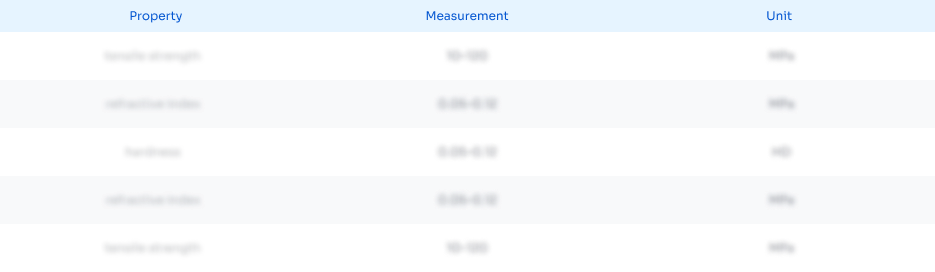
Abstract
Description
Claims
Application Information

- R&D
- Intellectual Property
- Life Sciences
- Materials
- Tech Scout
- Unparalleled Data Quality
- Higher Quality Content
- 60% Fewer Hallucinations
Browse by: Latest US Patents, China's latest patents, Technical Efficacy Thesaurus, Application Domain, Technology Topic, Popular Technical Reports.
© 2025 PatSnap. All rights reserved.Legal|Privacy policy|Modern Slavery Act Transparency Statement|Sitemap|About US| Contact US: help@patsnap.com