Method for parallel production of nutrient sugar, flavor cane juice and feedstuff by multistage membranes
A technology for feed raw materials and nutritional sugar, which is applied in the production of nutritional sugar, flavored cane juice and feed raw materials, can solve the problems that membrane technology is difficult to achieve, limited to white sugar, and the membrane separation efficiency is not fully exerted, and achieves the promotion of optimization and upgrading, The operation is simple and stable, and the effect of adapting to the fluctuation of incoming materials
- Summary
- Abstract
- Description
- Claims
- Application Information
AI Technical Summary
Problems solved by technology
Method used
Image
Examples
Embodiment 1
[0025] Example 1 Using "ultrafiltration-reverse osmosis" to prepare nutritional sugar, flavor cane juice and feed materials in parallel
[0026] The first step is the pretreatment of raw material juice and the separation of feed raw materials
[0027] Pump the sugarcane squeezed juice or the initial sugar factory juice into the filter press, and use a filter cloth with a pore size of 74 μm (200 mesh) as the filter carrier to remove large particles of impurities such as cane chips and cane pith in the raw juice The retentate sent back from the primary membrane separation process (ultrafiltration) is filtered again, and the filter residue is regularly discharged for feed production, and the filtered juice is used for ultrafiltration treatment. The operating temperature is 25°C, and the raw material barrel and filter press are sterilized with steam after filtration.
[0028] The second step of the first stage membrane separation to prepare clear cane juice
[0029] Extract 100L...
Embodiment 2
[0032] Example 2 Using "microfiltration-reverse osmosis" to prepare nutritional sugar, flavor cane juice and feed materials in parallel
[0033] The first step is the pretreatment of raw material juice and the separation of feed raw materials
[0034]Raise the temperature of the raw juice to 85°C and pump it into the air flotation clarifier to remove large particles of impurities such as sugarcane chips and pith in the raw juice, and float the retentate returned from the first-stage membrane separation process (microfiltration) again Separation treatment, collecting scum for feed production, and pretreated cane juice for microfiltration treatment. The operating temperature is 85°C. After clarification, the raw material barrel and air flotation clarifier are sterilized with steam.
[0035] The second step of the first stage membrane separation to prepare clear cane juice
[0036] Extract 100L of pretreated sugarcane juice at 80°C and pump it into the first-stage membrane sepa...
Embodiment 3
[0039] Example 3 Using "ultrafiltration-nanofiltration" to prepare nutritional sugar, flavor cane juice and feed materials in parallel
[0040] The first step is the pretreatment of sugarcane squeezed juice and the separation of feed ingredients
[0041] Heat up the sugarcane juice to 45°C and pump it into the filter press. Use a filter cloth with a pore size of 50 μm (300 mesh) as the filter carrier to remove large particles of impurities such as sugarcane chips and sugarcane pith in the raw juice. The retentate returned by the membrane separation process (ultrafiltration) is filtered again, and the filter residue is discharged for feed production, and the filtered juice is used for ultrafiltration treatment. The operating temperature is 45°C. After the filtration, the raw material barrel and filter press are sterilized with steam.
[0042] The second step of the first stage membrane separation to prepare clear cane juice
[0043] Extract 100L of pre-filtered 42°C sugarcane...
PUM
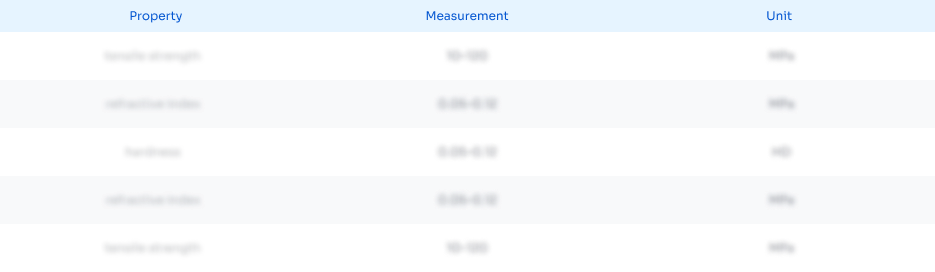
Abstract
Description
Claims
Application Information

- R&D
- Intellectual Property
- Life Sciences
- Materials
- Tech Scout
- Unparalleled Data Quality
- Higher Quality Content
- 60% Fewer Hallucinations
Browse by: Latest US Patents, China's latest patents, Technical Efficacy Thesaurus, Application Domain, Technology Topic, Popular Technical Reports.
© 2025 PatSnap. All rights reserved.Legal|Privacy policy|Modern Slavery Act Transparency Statement|Sitemap|About US| Contact US: help@patsnap.com