Method for preparing macroporous alkalescent anion exchange resin
A weakly basic anion and exchange resin technology, applied in anion exchange, ion exchange, chemical instruments and methods, etc., can solve the problems of low exchange rate, uneven pore size distribution, large proportion of small pores, etc., and achieve the goal of increasing the adsorption rate Effect
- Summary
- Abstract
- Description
- Claims
- Application Information
AI Technical Summary
Problems solved by technology
Method used
Image
Examples
Embodiment 1
[0014] (1) Styrene and divinylbenzene as monomers are washed with sodium hydroxide lotion, the polymerization inhibitor is removed, and dried for subsequent use after separation; wherein the quality of styrene is 48.5g, and the volume is 53.5ml, and divinylbenzene The mass of is 5.9g, the volume is 6.5ml;
[0015] (2) Add gelatin as a dispersant to 60ml of deionized water and soak for 2 hours, heat to 40°C; then add ammonium salt; wherein the quality of gelatin is 0.3g, and the quality of ammonium salt is 0.03g of the water quality;
[0016] (3) Mix monomer, benzoyl peroxide as initiator and butanol and lauryl alcohol as porogen, add in (2), after forming ball beads of suitable size, heat up to 75 ℃, keep warm for 4 hours; heat up to 85 ℃, keep warm for 6 hours, distill 2-3 times with deionized water, and filter with suction, then extract with acetone, dry at 50 ℃; sieve to obtain styrene- A copolymer of divinylbenzene, i.e. white ball; wherein the mass of benzoyl peroxide is...
Embodiment 2
[0023] (1) Styrene and divinylbenzene as monomers are washed with sodium hydroxide lotion, and the polymerization inhibitor is removed, and dried for subsequent use after separation; wherein the quality of styrene is 47.1g, and the volume is 51ml, and the amount of divinylbenzene The mass is 3.7g and the volume is 4ml;
[0024] (2) Add gelatin as a dispersant to 110ml of deionized water and soak for 3 hours, heat to 45°C; then add ammonium salt; wherein the quality of gelatin is 1.1g, and the quality of ammonium salt is 0.11g of the water quality;
[0025] (3) Mix monomer, benzoyl peroxide as initiator and butanol and lauryl alcohol as porogen, add in (2), after forming ball beads of suitable size, heat up to 78 ℃, keep warm for 5 hours; heat up to 88 ℃, keep warm for 8 hours, distill 2-3 times with deionized water, and filter with suction, then extract with acetone, dry at 55 ℃; sieve to obtain styrene- A copolymer of divinylbenzene, i.e. white ball; wherein the mass of benz...
Embodiment 3
[0032] (1) Styrene and divinylbenzene as monomers are washed with sodium hydroxide lotion, the polymerization inhibitor is removed, and dried for subsequent use after separation; wherein the quality of styrene is 41.9g, and the volume is 46.2ml, and divinylbenzene The mass is 6.6g and the volume is 7.2ml;
[0033] (2) Add gelatin as a dispersant to 160ml of deionized water and soak for 4 hours, heat to 50°C; then add ammonium salt; wherein the quality of gelatin is 2.4g, and the quality of ammonium salt is 0.16g of the water quality;
[0034] (3) Mix monomer, benzoyl peroxide as initiator and butanol and lauryl alcohol as porogen, join in (2), after forming ball beads of suitable size, heat up to 80 ℃, keep warm for 6 hours; heat up to 90 ℃, keep warm for 10 hours, distill 2-3 times with deionized water, and filter with suction, then extract with acetone, dry at 60 ℃; sieve to obtain styrene- A copolymer of divinylbenzene, i.e. white ball; wherein the mass of benzoyl peroxide...
PUM
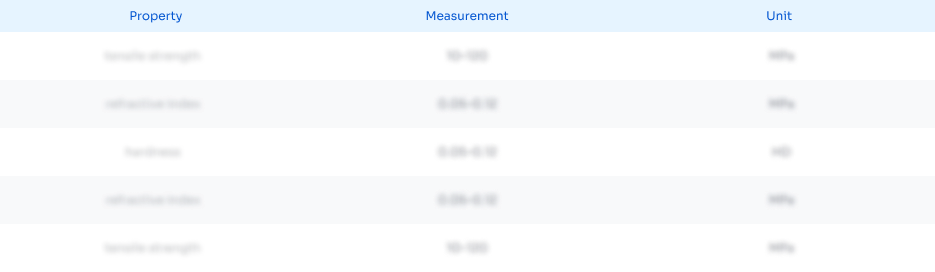
Abstract
Description
Claims
Application Information

- Generate Ideas
- Intellectual Property
- Life Sciences
- Materials
- Tech Scout
- Unparalleled Data Quality
- Higher Quality Content
- 60% Fewer Hallucinations
Browse by: Latest US Patents, China's latest patents, Technical Efficacy Thesaurus, Application Domain, Technology Topic, Popular Technical Reports.
© 2025 PatSnap. All rights reserved.Legal|Privacy policy|Modern Slavery Act Transparency Statement|Sitemap|About US| Contact US: help@patsnap.com