Catalytic conversion method used for raising gasoline octane number
A catalytic conversion method and gasoline octane number technology, applied in the petroleum industry, hydrocarbon oil treatment, hydrotreating process, etc., can solve problems such as insufficient product distribution, low isobutene content, and insufficient utilization of petroleum resources
- Summary
- Abstract
- Description
- Claims
- Application Information
AI Technical Summary
Problems solved by technology
Method used
Image
Examples
Embodiment 1
[0064] This example illustrates the use of the method provided by the present invention and the use of catalysts with different activity levels to increase the isobutene content in liquefied gas and the olefin content in gasoline in a medium-sized variable-diameter riser reactor.
[0065] The total height of the pre-lift section, the first reaction zone, the second reaction zone and the outlet zone of the reactor is 15 meters, the diameter of the pre-lift section is 0.025 meters, and its height is 1.5 meters; the diameter of the first reaction zone is 0.025 meters, and its height It is 4 meters; the diameter of the second reaction zone is 0.1 meters, and its height is 6.5 meters; the diameter of the outlet zone is 0.025 meters, and its height is 3 meters; is 45°; the base angle of the isosceles trapezoid in the longitudinal section of the junction of the second reaction zone and the outlet zone is 60°.
[0066] The feed oil A listed in preheated table 1 enters the reactor, and...
Embodiment 2
[0072] This example illustrates the use of the method provided by the present invention and the use of catalysts with different activity levels to increase the isobutene content in liquefied gas and the olefin content in gasoline in a medium-sized variable-diameter riser reactor.
[0073] The total height of the pre-lift section, the first reaction zone, the second reaction zone and the outlet zone of the reactor is 15 meters, the diameter of the pre-lift section is 0.025 meters, and its height is 1.5 meters; the diameter of the first reaction zone is 0.025 meters, and its height It is 4 meters; the diameter of the second reaction zone is 0.1 meters, and its height is 6.5 meters; the diameter of the outlet zone is 0.025 meters, and its height is 3 meters; is 45°; the base angle of the isosceles trapezoid in the longitudinal section of the junction of the second reaction zone and the outlet zone is 60°.
[0074] The raw material oil A listed in the table 1 of preheating enters ...
PUM
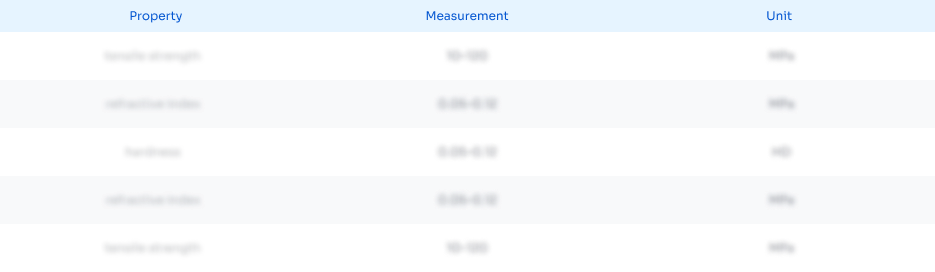
Abstract
Description
Claims
Application Information

- R&D
- Intellectual Property
- Life Sciences
- Materials
- Tech Scout
- Unparalleled Data Quality
- Higher Quality Content
- 60% Fewer Hallucinations
Browse by: Latest US Patents, China's latest patents, Technical Efficacy Thesaurus, Application Domain, Technology Topic, Popular Technical Reports.
© 2025 PatSnap. All rights reserved.Legal|Privacy policy|Modern Slavery Act Transparency Statement|Sitemap|About US| Contact US: help@patsnap.com