Method for preparing polyperfluorinated ethylene propylene resin
A technology of polyperfluoroethylene propylene and tetrafluoroethylene, which is applied in the field of chemical industry, can solve problems such as the change in the proportion of mixed monomers and the uneven distribution of polymerization product components, and achieve the effect of reducing the feeding time
- Summary
- Abstract
- Description
- Claims
- Application Information
AI Technical Summary
Problems solved by technology
Method used
Image
Examples
Embodiment 1
[0053] The batch radical emulsion preparation of the present invention is carried out in a 50L autoclave to prepare polyperfluoroethylene propylene resin. Add 30L of deionized water into the reaction kettle, heat up and boil, and keep the temperature constant for 80min. Then the air in the vapor space of the reactor was first replaced with nitrogen to an oxygen content of 20 ppm. Add 60g of 5wt% ammonium perfluorooctanoate aqueous solution into the reactor through a metering pump, and raise the temperature of the reactor to 85°C. 4.5Kg of initial mixed monomers (0.9Kg tetrafluoroethylene; 3.6Kg hexafluoropropylene) were added within 5min.
[0054] Start stirring, fully mix the mixed monomers in the reactor, then add 30g of 5wt% potassium persulfate solution to start the reaction. During the reaction, additional mixed monomers (tetrafluoroethylene:hexafluoropropylene=15:1 (molar ratio)) were used to maintain the pressure of the reactor at 3.5 MPa, and the reaction temperature...
Embodiment 2
[0056] The batch radical emulsion preparation of the present invention is carried out in a 50L autoclave to prepare polyperfluoroethylene propylene resin. Add 40L of deionized water into the reaction kettle, heat up and boil, and keep the temperature constant for 80min. Then the air in the vapor space of the reactor was first replaced with nitrogen to an oxygen content of 30 ppm. Add 11.4KG 7wt% potassium perfluorooctanoate aqueous solution into the reaction kettle through a metering pump, and raise the temperature of the reaction kettle to 110°C. 20Kg of initial mixed monomers (2.34Kg tetrafluoroethylene; 17.66Kg hexafluoropropylene) were added within 15min.
[0057] Turn on the stirring, fully mix the mixed monomers in the reactor, then add 1.2Kg of peroxysuccinic acid to start the reaction. During the reaction, additional mixed monomers (tetrafluoroethylene:hexafluoropropylene=19:5 (molar ratio)) were used to maintain the pressure of the reactor at 5.5 MPa, and the reacti...
Embodiment 3
[0059] The batch radical emulsion preparation of the present invention is carried out in a 50L autoclave to prepare polyperfluoroethylene propylene resin. Add 30L of deionized water into the reaction kettle, heat up and boil, and keep the temperature constant for 80min. Then the air in the vapor space of the reactor was first replaced with nitrogen to an oxygen content of 20 ppm. Add 60g of 5wt% ammonium perfluorooctanoate aqueous solution into the reactor through a metering pump, and raise the temperature of the reactor to 85°C. Add 6Kg of initial mixed monomers (3Kg tetrafluoroethylene; 3Kg hexafluoropropylene) within 5min.
[0060] Start stirring, fully mix the mixed monomers in the reactor, then add 30g of 5wt% potassium persulfate solution to start the reaction. During the reaction, additional mixed monomers (tetrafluoroethylene:hexafluoropropylene=3:1 (molar ratio)) were used to maintain the pressure of the reactor at 3.5 MPa, and the reaction temperature was 85°C. Af...
PUM
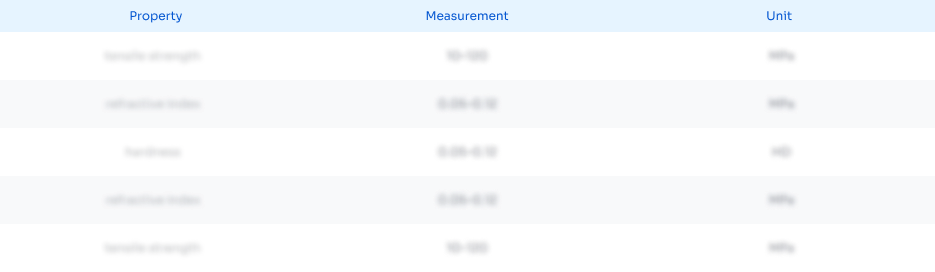
Abstract
Description
Claims
Application Information

- R&D
- Intellectual Property
- Life Sciences
- Materials
- Tech Scout
- Unparalleled Data Quality
- Higher Quality Content
- 60% Fewer Hallucinations
Browse by: Latest US Patents, China's latest patents, Technical Efficacy Thesaurus, Application Domain, Technology Topic, Popular Technical Reports.
© 2025 PatSnap. All rights reserved.Legal|Privacy policy|Modern Slavery Act Transparency Statement|Sitemap|About US| Contact US: help@patsnap.com