Device and method used for measuring axial and radial rigidity of magnetic suspension bearing
A technology of magnetic suspension bearing and radial stiffness, applied in the direction of mechanical bearing testing, etc., can solve the problems of difficult control of the measurement process, low stiffness accuracy, and unstable objects.
- Summary
- Abstract
- Description
- Claims
- Application Information
AI Technical Summary
Problems solved by technology
Method used
Image
Examples
Embodiment Construction
[0100] The invention provides a device for measuring the axial and radial stiffness of a magnetic suspension bearing, such as Figure 3a , 3b As shown, it includes three translation stages arranged perpendicularly to each other and their motion directions are also perpendicular to each other, which are X-direction precision electronically controlled translation platform 24, Y-direction precision electronically controlled translation platform 23, and Z-direction precision electronically controlled translation platform 9; and The laser displacement sensors (thick solid lines are lasers) used to measure the displacement of the precision electronically controlled displacement stage in the X, Y, and Z directions respectively are the laser displacement sensor 17 in the X direction, the laser displacement sensor 14 in the Y direction, and the laser displacement sensor in the Z direction. sensor 15;
[0101] The Y-direction precision electronically controlled displacement platform 23...
PUM
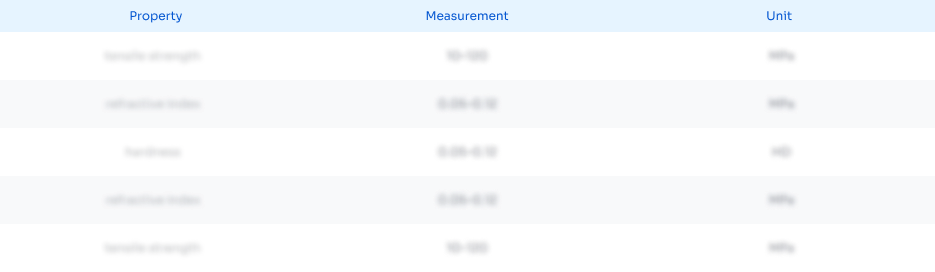
Abstract
Description
Claims
Application Information

- R&D Engineer
- R&D Manager
- IP Professional
- Industry Leading Data Capabilities
- Powerful AI technology
- Patent DNA Extraction
Browse by: Latest US Patents, China's latest patents, Technical Efficacy Thesaurus, Application Domain, Technology Topic, Popular Technical Reports.
© 2024 PatSnap. All rights reserved.Legal|Privacy policy|Modern Slavery Act Transparency Statement|Sitemap|About US| Contact US: help@patsnap.com