Cooling device for direct reduction iron
A cooling device and technology for reducing iron, applied in the direction of processing discharged materials, lighting and heating equipment, furnace components, etc., to achieve the effect of reducing equipment weight, simple structure, and good sealing effect
- Summary
- Abstract
- Description
- Claims
- Application Information
AI Technical Summary
Problems solved by technology
Method used
Image
Examples
Embodiment Construction
[0027] The present invention will be further described in detail below in conjunction with the accompanying drawings.
[0028] Such as figure 1 , figure 2 As shown, a cooling device for direct reduced iron includes a cooling cylinder 17, a ring gear 14 and a transmission device 6, the ring gear 14 is fixed on the outer circumference of the cooling cylinder 17, the ring gear 14 is connected with the transmission device 6, and the cooling cylinder One end of 17 is connected to the feed hopper 1, and the other end is connected to the kiln tail box 11. The end of the cooling cylinder 17 connected to the feed hopper 1 is provided with a kiln head box 4, and the outer circumference of the cooling cylinder 17 is arranged between the kiln head box 4. There is a head seal ring 5, a tail seal ring 12 is arranged between the outer circumference of the cooling cylinder 17 and the kiln tail box 11, an end seal ring 2 is arranged between the feed hopper 1 and the kiln head box 4, the hea...
PUM
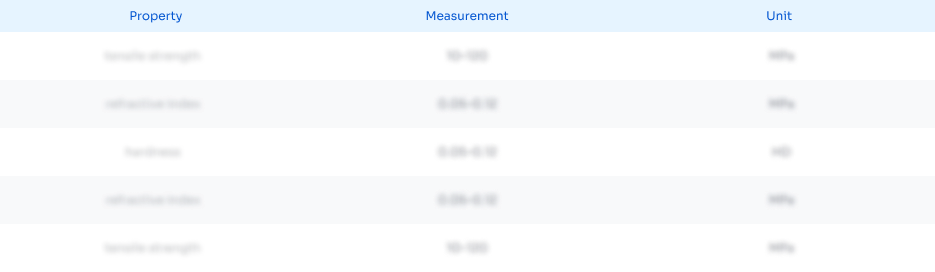
Abstract
Description
Claims
Application Information

- Generate Ideas
- Intellectual Property
- Life Sciences
- Materials
- Tech Scout
- Unparalleled Data Quality
- Higher Quality Content
- 60% Fewer Hallucinations
Browse by: Latest US Patents, China's latest patents, Technical Efficacy Thesaurus, Application Domain, Technology Topic, Popular Technical Reports.
© 2025 PatSnap. All rights reserved.Legal|Privacy policy|Modern Slavery Act Transparency Statement|Sitemap|About US| Contact US: help@patsnap.com