Process for preparing basic chromium sulfate by using waste chromium material
A technology of chromium sulfate and chromium material, applied in the field of inorganic salt recovery process and heavy metal treatment, can solve the problems of high treatment and production cost, complicated process, slow effect, etc., achieve low production cost, solve waste chromium pollution, and low investment. Effect
- Summary
- Abstract
- Description
- Claims
- Application Information
AI Technical Summary
Problems solved by technology
Method used
Examples
Embodiment 1
[0027] The technology that reclaims basic chromium sulfate from waste chrome material comprises the steps:
[0028] (1) Put 1000 Kg of chromium slag into the reaction kettle, add 150 Kg of sulfuric acid with a weight percentage of 98%, 70 Kg of sodium formate and 40 Kg of decolorizing clay, and at the same time, send steam at about 100°C to carry out acidification reaction treatment 3h, the acid gas and dust produced are pumped by the air duct to the gas purification device for treatment;
[0029] (2) After the acidification treatment, the slurry discharged from the reaction kettle is passed into the air pressure tank, and the slurry is pressed into the filter press for pressure filtration, and the solid impurities other than chromium components are discharged in the form of filter residue, while the filter press liquid is After being collected by the slurry tank, it is stored in the waste chrome liquid storage tank;
[0030] (3) The waste chrome solution and press filtrate p...
Embodiment 2
[0033] The technology that reclaims basic chromium sulfate from waste chrome material comprises the steps:
[0034] (1) Put 1000 Kg of chromium slag into the reaction kettle, add 80 Kg of sulfuric acid with a weight percentage of 98%, 50 Kg of sodium formate and 20 Kg of decolorizing clay, and simultaneously send in steam at about 95°C to carry out The acidification reaction is treated for 4 hours, and the acid gas and dust generated are pumped through the air duct to the gas purification device for treatment;
[0035] (2) After the acidification treatment, the slurry discharged from the reaction kettle is passed into the air pressure tank, and the slurry is pressed into the filter press for pressure filtration, and the solid impurities other than chromium components are discharged in the form of filter residue, while the filter press liquid is After being collected by the slurry tank, it is stored in the waste chrome liquid storage tank;
[0036] (3) The waste chrome solutio...
Embodiment 3
[0039] The technology that reclaims basic chromium sulfate from waste chrome material comprises the steps:
[0040] (1) Put 1000 Kg of chromium slag into the reaction kettle, add 160 Kg of sulfuric acid with a weight percentage of 98%, 80 Kg of sodium formate and 50 Kg of bleaching clay, and at the same time, send steam at about 110°C to carry out acidification reaction After 2 hours of treatment, the acid gas and dust produced are pumped through the air duct to the gas purification device for treatment;
[0041] (2) After the acidification treatment, the slurry discharged from the reaction kettle is passed into the air pressure tank, and the slurry is pressed into the filter press for pressure filtration, and the solid impurities other than chromium components are discharged in the form of filter residue, while the filter press liquid is After being collected by the slurry tank, it is stored in the waste chrome liquid storage tank;
[0042] (3) The waste chrome solution and ...
PUM
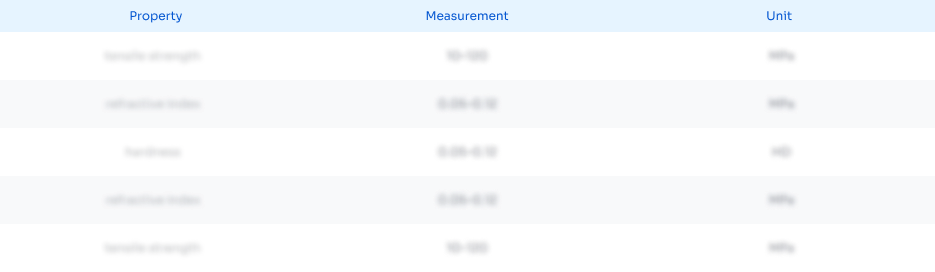
Abstract
Description
Claims
Application Information

- R&D
- Intellectual Property
- Life Sciences
- Materials
- Tech Scout
- Unparalleled Data Quality
- Higher Quality Content
- 60% Fewer Hallucinations
Browse by: Latest US Patents, China's latest patents, Technical Efficacy Thesaurus, Application Domain, Technology Topic, Popular Technical Reports.
© 2025 PatSnap. All rights reserved.Legal|Privacy policy|Modern Slavery Act Transparency Statement|Sitemap|About US| Contact US: help@patsnap.com