Gain scheduling control method for magnetic suspension molecular pump
A technology of gain scheduling control and molecular pumps, which is applied in pump control, pumps, axial flow pumps, etc., can solve problems such as the difficulty of rotor vibration suppression, and achieve the effect of improving stability
- Summary
- Abstract
- Description
- Claims
- Application Information
AI Technical Summary
Problems solved by technology
Method used
Image
Examples
specific Embodiment approach
[0027] The following provides a specific implementation of a magnetic levitation molecular pump gain scheduling control method according to the present invention, including the following steps:
[0028] (1) The magnetic levitation molecular pump controller 17 controls the speed up of the magnetic levitation molecular pump motor, detects the rotor displacement through the rotor displacement detection device 16 , and detects the rotor speed through the rotor speed detection device 15 .
[0029] Generally, when the rotor speed is less than 40 rpm, it is low speed; when the rotor speed is between 40 rpm and 80 rpm, it is medium and low speed; when the rotor speed is between 80 rpm and 140 rpm, it is Medium speed; when the rotor speed is between 140 rpm and 220 rpm, it is medium and high speed; when the rotor speed is greater than 220 rpm, it is high speed, and the rotor speed is at high speed.
[0030] The rotor displacement detection device 16 and the rotor speed detection device...
PUM
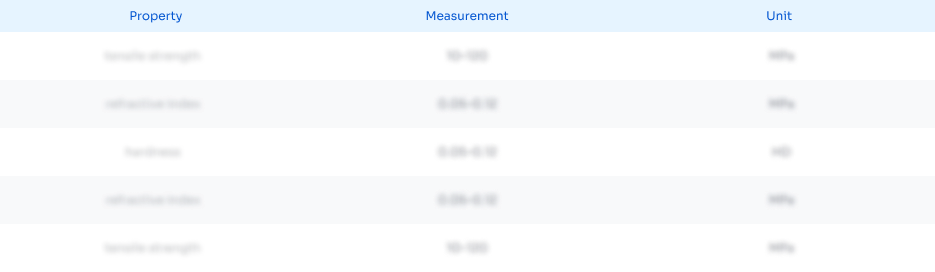
Abstract
Description
Claims
Application Information

- R&D
- Intellectual Property
- Life Sciences
- Materials
- Tech Scout
- Unparalleled Data Quality
- Higher Quality Content
- 60% Fewer Hallucinations
Browse by: Latest US Patents, China's latest patents, Technical Efficacy Thesaurus, Application Domain, Technology Topic, Popular Technical Reports.
© 2025 PatSnap. All rights reserved.Legal|Privacy policy|Modern Slavery Act Transparency Statement|Sitemap|About US| Contact US: help@patsnap.com