Cleaning sheet, conveyance member with cleaning function, cleaning method of substrate processing apparatus, and substrate processing apparatus
A technology for cleaning sheets and components, applied in the direction of cleaning methods using tools, cleaning methods and utensils, chemical instruments and methods, etc., can solve problems such as insufficiency, and achieve good efficiency, excellent foreign matter removal performance, and excellent transfer performance.
- Summary
- Abstract
- Description
- Claims
- Application Information
AI Technical Summary
Problems solved by technology
Method used
Image
Examples
Embodiment 1
[0101] With respect to 100 parts of acrylic polymer (weight average molecular weight: 700,000) obtained from a monomer mixture containing 75 parts of 2-ethylhexyl acrylate, 20 parts of methyl acrylate, and 5 parts of acrylic acid, uniformly mix 200 parts of polyethylene glycol 200 dimethacrylate (manufactured by Shin-Nakamura Chemical, trade name: NK Ester 4G), 3 parts of polyisocyanate compound (manufactured by Nippon Polyurethane Industry, trade name: Coronate L), and as a photopolymerization initiator 3 parts of benzil dimethyl ketal (manufactured by Ciba Specialty Chemicals, trade name: Irgacure 651) was used to prepare UV-curable adhesive solution A.
[0102] On the other hand, 73 parts of 2-ethylhexyl acrylate, 10 parts of n-butyl acrylate, N , 15 parts of N-dimethylacrylamide, 5 parts of acrylic acid, 0.15 parts of 2,2'-azobisisobutyronitrile as a polymerization initiator, and 100 parts of ethyl acetate were prepared to make a total of 200g, while introducing nitrogen g...
Embodiment 2
[0118] 14.8 g of polyether diamine (manufactured by Sun Technochemical, XTJ-510) and 4,4'-DPE were mixed in 133 g of N,N-dimethylacetamide (DAMc) at 70° C. in an environment under a nitrogen stream. (DDE)8.45g and 10.0g of pyromellitic dianhydride (PMDA) were made to react, and polyamic-acid solution A was obtained.
[0119] After cooling, the polyamic acid solution A was coated on the etched surface of an 8-inch silicon wafer with a spin coater, and dried at 90° C. for 20 minutes to obtain a polyamic acid-attached transport member (2).
[0120] The conveying member (2) agglomerated with polyamic acid was heat-treated at 300° C. for 2 hours in a nitrogen atmosphere to form a polyimide film with a thickness of 30 μm, thereby obtaining a conveying member (2) with a cleaning function.
[0121] The average surface roughness Ra of the cleaning layer of the conveying member (2) with a cleaning function was 0.54 μm.
[0122] The cleaning layer of the transport member (2) with a clea...
Embodiment 3
[0130] On the entire surface of the mirror surface of an 8-inch silicon wafer, a laser mark for ID identification specified in the SEMI standard is formed on the entire surface, and the following is obtained. image 3 wafers (3). Using the polyamic acid solution A described in Example 2, it was coated on the mirror surface of the wafer (3) with a spin coater, and dried at 120° C. for 10 minutes to obtain a transport member (3) with polyamic acid.
[0131] The transport member (3) with polyamic acid was heat-treated at 300° C. for 2 hours in a nitrogen atmosphere to form a polyimide film with a thickness of 8 μm, and a transport member (3) with a cleaning function was obtained.
[0132] The average surface roughness Ra of the cleaning layer of the conveyance member (3) with a cleaning function was 0.34 μm.
[0133]The cleaning layer of the transport member (3) with a cleaning function was peeled off from the silicon wafer, and the 180° peel adhesion to the silicon wafer (mirro...
PUM
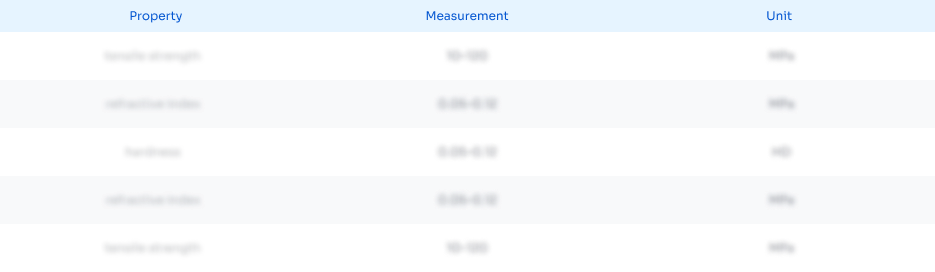
Abstract
Description
Claims
Application Information

- R&D
- Intellectual Property
- Life Sciences
- Materials
- Tech Scout
- Unparalleled Data Quality
- Higher Quality Content
- 60% Fewer Hallucinations
Browse by: Latest US Patents, China's latest patents, Technical Efficacy Thesaurus, Application Domain, Technology Topic, Popular Technical Reports.
© 2025 PatSnap. All rights reserved.Legal|Privacy policy|Modern Slavery Act Transparency Statement|Sitemap|About US| Contact US: help@patsnap.com