Manufacturing method for end socket module of quenching heat exchanger
A technology of quenching heat exchanger and manufacturing method, which is applied in the manufacturing field of the head module of the quenching heat exchanger, which can solve the problems of long order cycle, poor stress resistance of the head, shortening the operation cycle of the cracking furnace, etc., and achieve performance index improvement , stable performance, satisfying the effect of long-term operation
- Summary
- Abstract
- Description
- Claims
- Application Information
AI Technical Summary
Problems solved by technology
Method used
Image
Examples
Embodiment Construction
[0049] The present invention will be further described in detail below in conjunction with the accompanying drawings and embodiments.
[0050] Such as figure 1 and figure 2 As shown, the manufacturing method of the quenching heat exchanger head module is as follows:
[0051] A) the steel housing 1 of the prefabricated quenching heat exchanger head module;
[0052] B) Prepare the materials used for the prefabricated insert 2 according to the following formula, and the materials used for the insert include base materials and ingredients.
[0053] Wherein, each component content in base material is weight content;
[0054]
[0055] The consumption of each component is based on the total amount of the base material in the batching, and its weight composition is as follows:
[0056]
[0057]
[0058] The consumption of each component in the batching is calculated according to the total amount of the filler base material.
[0059] Mix the base material and ingredients...
PUM
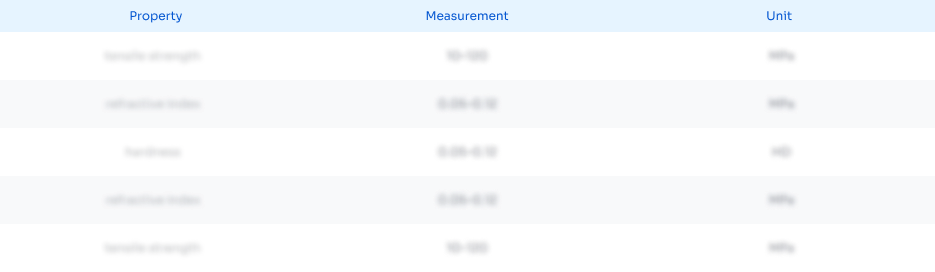
Abstract
Description
Claims
Application Information

- R&D
- Intellectual Property
- Life Sciences
- Materials
- Tech Scout
- Unparalleled Data Quality
- Higher Quality Content
- 60% Fewer Hallucinations
Browse by: Latest US Patents, China's latest patents, Technical Efficacy Thesaurus, Application Domain, Technology Topic, Popular Technical Reports.
© 2025 PatSnap. All rights reserved.Legal|Privacy policy|Modern Slavery Act Transparency Statement|Sitemap|About US| Contact US: help@patsnap.com