Waste heat power generation device capable of obtaining waste gas in multistage from sintering machine and cooling machine in steel plant
A technology of waste heat power generation and sintering machine, which is applied in the direction of steam engine installation, waste heat treatment, machine/engine, etc. It can solve problems such as not considering the composition of sintering machine flue gas, affecting boiler operation and service life, and pipe perforation, so as to avoid low temperature Acid dew point corrosion problem, save civil engineering amount, and reduce weight
- Summary
- Abstract
- Description
- Claims
- Application Information
AI Technical Summary
Problems solved by technology
Method used
Image
Examples
Embodiment Construction
[0021] exist figure 1 and figure 2 In the schematic diagram of the front view of the sintering machine and cooler multi-stage exhaust gas waste heat power generation device shown in the iron and steel plant, the sintering machine components include the sintering machine 3, the tail main flue 29, the electrostatic precipitator 2 and the chimney 1, all of which are for existing technology. The above sintering integrated waste heat recovery device mainly includes a cyclone superheater 6, a sintering machine waste heat boiler 5 and pipelines, wherein the cyclone superheater 6 and sintering machine waste heat boiler 5 are arranged in an integrated form and share a common foundation. The cyclone superheater 6 adopts the structure of the Chinese utility model patent No. ZL2010 2 0554915.4. The above-mentioned equipment has the following connections: the main flue 29 at the tail of the sintering machine is connected to the upper side opening of the cyclone superheater 6, the upper ...
PUM
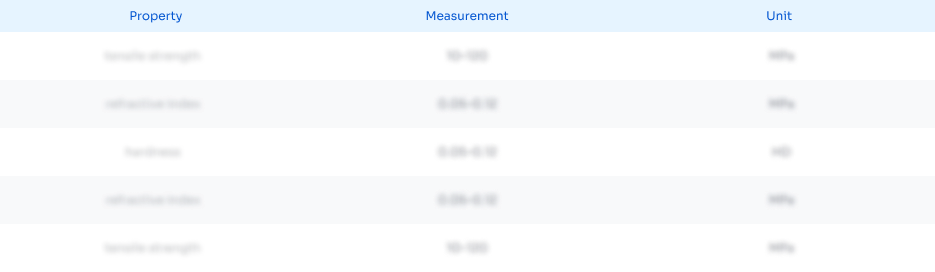
Abstract
Description
Claims
Application Information

- Generate Ideas
- Intellectual Property
- Life Sciences
- Materials
- Tech Scout
- Unparalleled Data Quality
- Higher Quality Content
- 60% Fewer Hallucinations
Browse by: Latest US Patents, China's latest patents, Technical Efficacy Thesaurus, Application Domain, Technology Topic, Popular Technical Reports.
© 2025 PatSnap. All rights reserved.Legal|Privacy policy|Modern Slavery Act Transparency Statement|Sitemap|About US| Contact US: help@patsnap.com