Adjusting boiler of low pressure section at cement kiln end
A low-pressure section and cement kiln technology, applied in the field of boilers, can solve problems such as waste of waste heat resources, and achieve the effect of improving power generation capacity and reasonable structure
- Summary
- Abstract
- Description
- Claims
- Application Information
AI Technical Summary
Problems solved by technology
Method used
Image
Examples
Embodiment Construction
[0010] A regulating boiler in the low-pressure section at the end of a cement kiln. In the same waste heat boiler at the end of the kiln, two steam-water systems with different pressure levels, high pressure and low pressure, are installed. The high-pressure system 1 uses the waste heat generated by the high-pressure main steam to directly enter the gas turbine 2 for power generation. Boiler, the exhaust gas temperature is controlled at about 220°C; the low-pressure system 3 generates low-pressure steam for recovering the waste heat of the waste gas, and supplies most of the low-pressure steam as supplementary steam to the steam turbine 2, and further reduces the exhaust gas temperature (below 180°C) kiln The tail low pressure section regulates the boiler. The range of regulating boiler working pressure is 0.5MPa~2.35MPa.
[0011] Also in the figure are a high-pressure drum 4, a low-pressure drum 6, a generator 7, a condenser 8, a condensate pump 9, a drain tank 10, a drain ta...
PUM
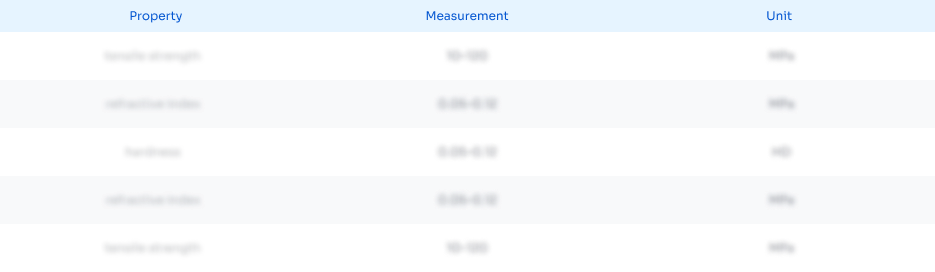
Abstract
Description
Claims
Application Information

- R&D
- Intellectual Property
- Life Sciences
- Materials
- Tech Scout
- Unparalleled Data Quality
- Higher Quality Content
- 60% Fewer Hallucinations
Browse by: Latest US Patents, China's latest patents, Technical Efficacy Thesaurus, Application Domain, Technology Topic, Popular Technical Reports.
© 2025 PatSnap. All rights reserved.Legal|Privacy policy|Modern Slavery Act Transparency Statement|Sitemap|About US| Contact US: help@patsnap.com