Universal post processing method for multi-axis numerical control machine tool
A CNC machine tool and post-processing technology, applied in the direction of digital control, electrical program control, etc., to achieve the effect of simplifying the process, eliminating long calculation time, and improving speed and efficiency
- Summary
- Abstract
- Description
- Claims
- Application Information
AI Technical Summary
Problems solved by technology
Method used
Image
Examples
Embodiment Construction
[0022] The present invention will be further described below in conjunction with the accompanying drawings and specific embodiments.
[0023] The general post-processing method for multi-axis machine tools includes the following steps:
[0024] (1) Analyze and measure the relative positional relationship between the moving parts of the multi-axis CNC machine tool, and establish the kinematic transformation chain of the machine tool. The kinematic chain of the machine tool includes the kinematic chain Q of the tool to the machine tool MT and workpiece to machine kinematic chain T WM , the direction vector and position of the tool position point are transformed by motion to obtain the direction vector and position information of the machining point on the workpiece. The relationship is shown in the following equations:
[0025] Q MW ...
PUM
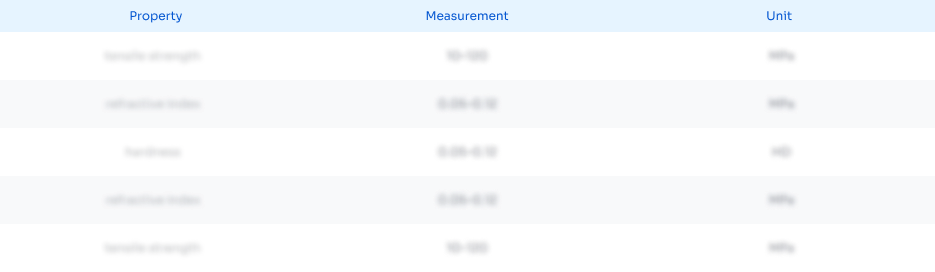
Abstract
Description
Claims
Application Information

- Generate Ideas
- Intellectual Property
- Life Sciences
- Materials
- Tech Scout
- Unparalleled Data Quality
- Higher Quality Content
- 60% Fewer Hallucinations
Browse by: Latest US Patents, China's latest patents, Technical Efficacy Thesaurus, Application Domain, Technology Topic, Popular Technical Reports.
© 2025 PatSnap. All rights reserved.Legal|Privacy policy|Modern Slavery Act Transparency Statement|Sitemap|About US| Contact US: help@patsnap.com