Production process of double-point non-woven fusible interlining
A production process and non-woven technology, which is applied in the production process field of double-point non-woven hot-melt interlining, can solve the problems of increasing energy consumption, prolonging cooling time, and poor cooling effect, so as to improve production efficiency, increase peel strength, and cool good effect
- Summary
- Abstract
- Description
- Claims
- Application Information
AI Technical Summary
Benefits of technology
Problems solved by technology
Method used
Image
Examples
Embodiment Construction
[0022] Such as figure 1 As shown, the production process of double-point nonwoven hot-melt interlining includes the following steps in turn:
[0023] A). In terms of mass, 43% nylon fiber and 57% polyester fiber are used as raw materials, and the raw materials are heated and hot-rolled by a hot rolling mill to bond nylon fibers and polyester fibers to form a non-woven base fabric ; The non-woven base fabric formed by hot rolling is 18g / m 2 , which not only meets the thickness and strength requirements, but also reduces the cost. The proportion mixing of nylon fiber and polyester fiber not only improves the softness of the interlining, but also reduces the cost.
[0024] B). The non-woven base fabric was softened with silicone oil and then inspected; the silicone oil treatment further improved the softness.
[0025] C). After passing the inspection, the cloth will be dropped;
[0026] D). After the cloth is dropped, the double-point coating is carried out. First, the base s...
PUM
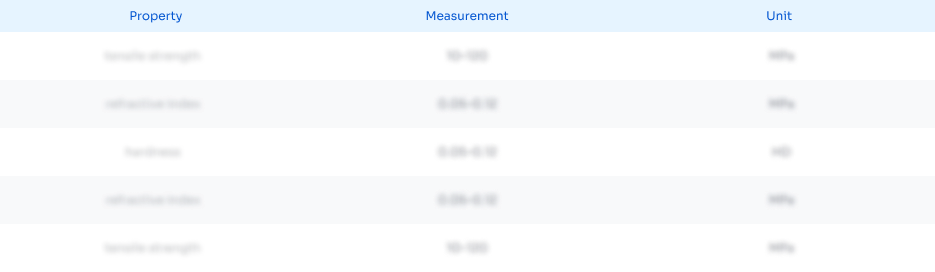
Abstract
Description
Claims
Application Information

- R&D
- Intellectual Property
- Life Sciences
- Materials
- Tech Scout
- Unparalleled Data Quality
- Higher Quality Content
- 60% Fewer Hallucinations
Browse by: Latest US Patents, China's latest patents, Technical Efficacy Thesaurus, Application Domain, Technology Topic, Popular Technical Reports.
© 2025 PatSnap. All rights reserved.Legal|Privacy policy|Modern Slavery Act Transparency Statement|Sitemap|About US| Contact US: help@patsnap.com