Preparation process for 4- bromo phenyl hydrazine
A preparation process, bromophenylhydrazine technology, applied in the field of preparation of 4-bromophenylhydrazine, can solve the problems of poor product quality, low product purity, high production cost, etc.
- Summary
- Abstract
- Description
- Claims
- Application Information
AI Technical Summary
Problems solved by technology
Method used
Examples
Embodiment 1
[0015] 2.76 g of 4-nitroaniline, 5 ml of 10N hydrochloric acid, stirred and heated to 60-80 °C, after the 4-nitroaniline was completely dissolved, cooled to below 0 °C, and added sodium nitrite solution (13.8 g of sodium nitrite dissolved in 30ml of water), react at 0-5°C for 5 minutes, filter to remove residue, and obtain a diazonium salt solution.
[0016] Weigh 2.76 grams of sodium metabisulfite, dissolve it in 25ml of water, then add 5ml of 10N sodium hydroxide to make a sodium metabisulfite alkali solution, add the above diazonium salt solution at 5-10°C, adjust the pH to 7-8, and adjust the pH to 7-8 at 15-35 It was reacted at ℃ for 30 minutes, then 10ml of 10N hydrochloric acid was added, and after reacting at 50-90℃ for 30 minutes, it was cooled to room temperature and filtered. Treat in 125ml of 10N hydrochloric acid at 55-90°C for 30 minutes, filter again, collect the filtrate, and dry to obtain 4-nitrophenylhydrazine hydrochloride product (99.5%).
[0017] The same...
Embodiment 2
[0019] Add 3.44 grams of 4-sulfonylaminoaniline, 10 ml of water, and 5 ml of 10N hydrochloric acid into a 100 ml flask, stir to dissolve, and after cooling to below 0°C, add sodium nitrite solution (composed of 1.38 grams of sodium nitrite and 2.76 ml of water) , react at 0-5°C for 5 minutes, filter to remove residue, and obtain diazonium salt solution.
[0020] Sodium pyrosulfite 6.4g, water 25ml, 10N sodium hydroxide 5ml, stirring and dissolving to make sodium pyrosulfite alkaline solution, after cooling to 10-20°C, add the above diazonium salt solution, adjust the pH to 7-8, at 20-30 After reacting at ℃ for 30 minutes, add 10ml of 10N hydrochloric acid and heat to 90-103℃. After reacting for 30 minutes, add 0.1 g of activated carbon, or filter the residue and cool to 10℃ to filter, purify, and dry to obtain the product. The instrument detects that its purity is 99.5%.
[0021] In the same way, 3-fluorophenylhydrazine, 4-sulfonic acid phenylhydrazine, 2- and 4-carboxyphenyl...
Embodiment 3
[0023] 2 grams of 4-methoxyaniline, 4 ml of water, 3.8 ml of 10N hydrochloric acid, stir to dissolve, cool to 0 ° C, add nitrous acid solution (composed of 1.12 g of sodium nitrite and 2.12 ml of water), at 0-5 ° C After reacting for 5 minutes, filter to obtain diazonium salt solution.
[0024] 6.4 grams of sodium pyrosulfite, 10 ml of water, 2.5 ml of 10N sodium hydroxide were stirred to form a sodium pyrosulfite alkaline solution, cooled to 10-20°C, and the above-mentioned diazonium salt solution was added. React at 20-35° C., pH=6-8 for 30 minutes, filter, and collect the filtrate.
[0025] Dissolve the above filtrate in 3ml of water, add 0.3ml of glacial acetic acid and 0.3g of zinc powder at 50°C, raise the temperature to 70-90°C, react for 5 minutes, filter to remove residue, add 2ml of 10N hydrochloric acid to the filtrate, Collect the filtrate and purify it with ethanol to obtain 4-methoxyphenylhydrazine, whose purity is 99.1% as detected by high-pressure liquid chrom...
PUM
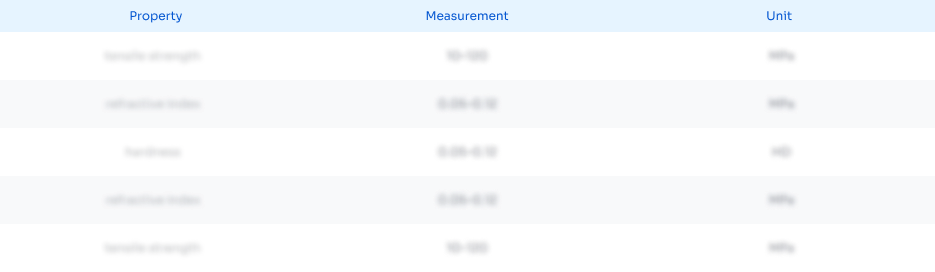
Abstract
Description
Claims
Application Information

- Generate Ideas
- Intellectual Property
- Life Sciences
- Materials
- Tech Scout
- Unparalleled Data Quality
- Higher Quality Content
- 60% Fewer Hallucinations
Browse by: Latest US Patents, China's latest patents, Technical Efficacy Thesaurus, Application Domain, Technology Topic, Popular Technical Reports.
© 2025 PatSnap. All rights reserved.Legal|Privacy policy|Modern Slavery Act Transparency Statement|Sitemap|About US| Contact US: help@patsnap.com