Redundancy error-proofing method of robot
A robot and error-proof technology, applied in the direction of manipulators, manufacturing tools, etc., can solve problems such as missed detection, sensor damage, etc.
- Summary
- Abstract
- Description
- Claims
- Application Information
AI Technical Summary
Problems solved by technology
Method used
Image
Examples
Embodiment Construction
[0013] In the following, the embodiment of the present invention will be described in detail by taking a welding robot as an example in conjunction with the accompanying drawings.
[0014] Such as figure 1 As shown, when the robot using this redundant error-proofing method is working, it first performs step S100: set the task execution condition, the task execution condition is the state of the sensor in the state of no missing parts; then execute step S110, read the state of the sensor , then execute step S120, compare the state of the read sensor with the set task execution condition, if the read sensor state is not the same as the set task execution condition, then execute step S130, the robot does not perform the operation task and Carry out alarm display. The alarm information at this time indicates that there are missing parts on the welding assembly. The operator should check the welding assembly in time and install the missing parts; such as the read sensor status and ...
PUM
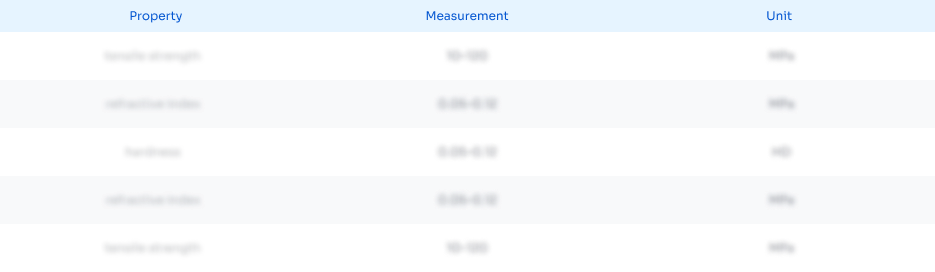
Abstract
Description
Claims
Application Information

- R&D
- Intellectual Property
- Life Sciences
- Materials
- Tech Scout
- Unparalleled Data Quality
- Higher Quality Content
- 60% Fewer Hallucinations
Browse by: Latest US Patents, China's latest patents, Technical Efficacy Thesaurus, Application Domain, Technology Topic, Popular Technical Reports.
© 2025 PatSnap. All rights reserved.Legal|Privacy policy|Modern Slavery Act Transparency Statement|Sitemap|About US| Contact US: help@patsnap.com