Precleaning process of silicon wafer
A technology for pre-cleaning and silicon wafers, applied in cleaning methods and utensils, sustainable manufacturing/processing, cleaning methods using liquids, etc., can solve the problem of large amount of hydrogen peroxide, unstable hydrogen peroxide, poor cleaning effect, etc. problems, to achieve high yield, high photoelectric conversion efficiency, and low surface tension
- Summary
- Abstract
- Description
- Claims
- Application Information
AI Technical Summary
Problems solved by technology
Method used
Image
Examples
Embodiment 1
[0024] a) Immersion treatment, put the silicon wafer into the immersion solution, heat the immersion solution to 75°C, and immerse for 600s, wherein the immersion solution includes isopropanol accounting for 6% of the total volume and additives accounting for 8‰ of the total volume;
[0025] b) Rinse once, use deionized water to rinse the silicon wafer after soaking, the rinse time is 300s, and the temperature of deionized water is 70°C;
[0026] c) Oxidation treatment, put the silicon wafer rinsed once into the oxidizing solution, heat the oxidizing solution to 59°C, and oxidize for 500 seconds, wherein the oxidizing solution includes ammonia water accounting for 5% of the total volume, and ammonia water accounting for 8% of the total volume. Hydrogen peroxide, the rest is water;
[0027] d) Second rinse, using deionized water to rinse the oxidized silicon wafer for 300s, wherein the temperature of the deionized water is 70°C.
[0028] Through actual operation, the process o...
Embodiment 2
[0031] a) Immersion treatment, put the silicon wafer into the immersion solution, heat the immersion solution to 55°C, and immerse for 200s, wherein the immersion solution includes isopropanol accounting for 2% of the total volume and additives accounting for 2‰ of the total volume;
[0032] b) Rinse once, use deionized water to rinse the silicon wafer after soaking, the rinse time is 100s, and the temperature of deionized water is 40°C;
[0033] c) Oxidation treatment, put the silicon wafer rinsed once into the oxidizing solution, heat the oxidizing solution to 50°C, and oxidize for 200s, wherein the oxidizing solution includes 2% of the total volume of ammonia water, 3% of the total volume of Hydrogen peroxide, the rest is water;
[0034] d) Second rinse, using deionized water to rinse the oxidized silicon wafer for 100s, wherein the temperature of the deionized water is 40°C.
[0035] Through actual operation, the process of the present invention compares with traditional ...
Embodiment 3
[0039] a) Immersion treatment, put the silicon wafer into the immersion solution, heat the immersion solution to 60°C, and immerse for 400s, wherein the immersion solution includes isopropanol accounting for 4% of the total volume and additives accounting for 6‰ of the total volume;
[0040] b) Rinse once, use deionized water to rinse the silicon wafer after soaking, the rinse time is 200s, and the temperature of deionized water is 55°C;
[0041] c) Oxidation treatment, put the silicon wafer rinsed once into the oxidizing solution, heat the oxidizing solution to 55°C, and oxidize for 340s, wherein the oxidizing solution includes 4% of the total volume of ammonia water, 5% of the total volume of Hydrogen peroxide, the rest is water;
[0042] d) Second rinse, using deionized water to rinse the oxidized silicon wafer, the rinse time is 200s, wherein the temperature of the deionized water is 56°C.
[0043] Through actual operation, the process of the present invention compares wi...
PUM
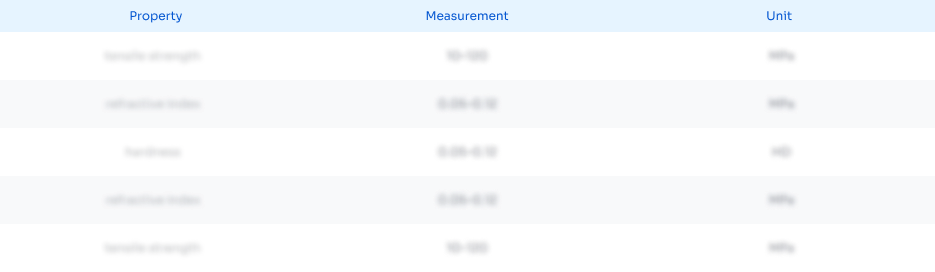
Abstract
Description
Claims
Application Information

- R&D
- Intellectual Property
- Life Sciences
- Materials
- Tech Scout
- Unparalleled Data Quality
- Higher Quality Content
- 60% Fewer Hallucinations
Browse by: Latest US Patents, China's latest patents, Technical Efficacy Thesaurus, Application Domain, Technology Topic, Popular Technical Reports.
© 2025 PatSnap. All rights reserved.Legal|Privacy policy|Modern Slavery Act Transparency Statement|Sitemap|About US| Contact US: help@patsnap.com