Production technology of finish-rolled ribbed bars
A production process and technology for finishing threads, applied in the field of production technology of finishing threaded steel bars, can solve the problems of prolonged production cycle, high production costs, low product performance indicators, etc., and achieve production cost reduction, product quality improvement, and performance indicators. excellent effect
- Summary
- Abstract
- Description
- Claims
- Application Information
AI Technical Summary
Problems solved by technology
Method used
Image
Examples
Embodiment 1
[0036] Brand: PSB830, specification: Φ32mm.
[0037] Billet heating→rolling→on-line controlled cooling→natural cooling on upper cooling bed→length cutting→stack cooling.
[0038] ●The chemical composition is shown in Table 3, and the raw material is: 150×150×12000mm continuous casting billet.
[0039] Table 3 Chemical Composition of Finished Rebars Unit: (%)
[0040] C
Si
mn
V
P
S
Fe
0.40
1.60
0.94
0.11
0.016
0.009
margin
[0041] The billet is subjected to three-stage heating treatment, in which the temperature in the preheating section is ≤850°C, the temperature in the heating section is 1100°C-1170°C, the temperature in the soaking section is 1090°C-1160°C, and the total heating time is 100-150 minutes;
[0042] ●In the rolling process, a total of 14 rolling mills are used, the starting rolling temperature is 1020-1100°C, and the final rolling speed is controlled at 4.0-5.5m / s;
[...
Embodiment 2
[0049] Brand: PSB930, specification: Φ25mm.
[0050] Billet heating→rolling→on-line controlled cooling→natural cooling on upper cooling bed→length cutting→stack cooling.
[0051] ●The chemical composition is shown in Table 5, and the raw material is: 150×150×12000mm continuous casting billet.
[0052] Table 5 Chemical Composition of Finished Rebars Unit: (%)
[0053] C
Si
mn
V
P
S
Fe
0.42
1.57
0.86
0.10
0.022
0.008
margin
[0054] The billet is subjected to three-stage heating treatment, in which the temperature of the preheating section is ≤850°C, the temperature of the heating section is 1090°C-1160°C, the temperature of the soaking section is 1080°C-1150°C, and the total heating time is 100-150 minutes;
[0055]●In the rolling process, a total of 14 rolling mills are used, the starting rolling temperature is 1000-1080 ℃, and the final rolling speed is controlled at 6.0-7.5m / s;
[0...
PUM
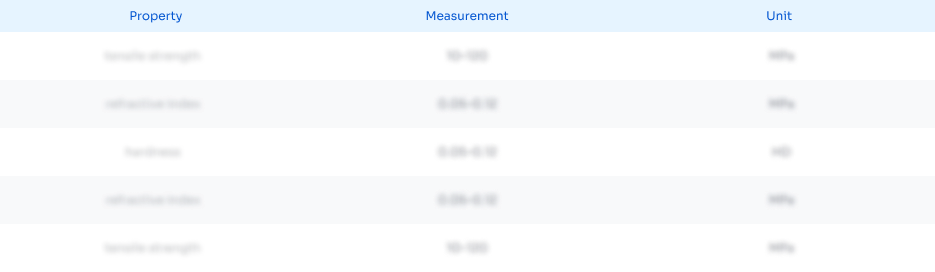
Abstract
Description
Claims
Application Information

- Generate Ideas
- Intellectual Property
- Life Sciences
- Materials
- Tech Scout
- Unparalleled Data Quality
- Higher Quality Content
- 60% Fewer Hallucinations
Browse by: Latest US Patents, China's latest patents, Technical Efficacy Thesaurus, Application Domain, Technology Topic, Popular Technical Reports.
© 2025 PatSnap. All rights reserved.Legal|Privacy policy|Modern Slavery Act Transparency Statement|Sitemap|About US| Contact US: help@patsnap.com