Die for casting dry type transformer coil
A technology for dry-type transformers and moulds, which is applied in the manufacture of coils, etc., which can solve the problems that the machining accuracy of lathes and milling machines cannot meet the technical requirements, increase mold processing costs and processing cycles, and limit the processing distance of milling machines, etc., to reduce clamping , reduce vibration, reduce the effect of processing difficulty
- Summary
- Abstract
- Description
- Claims
- Application Information
AI Technical Summary
Problems solved by technology
Method used
Image
Examples
Embodiment Construction
[0012] Such as figure 1 , 2 As shown in and 3, a dry-type transformer coil casting mold is composed of a left half-shell 4 and a right half-shell 5. Bolts I connect the left half-shell 4 and the right half-shell 5 into one body, and the left half-shell 4 and the right half-shell 5 There is a sealing groove Ⅰ on the contact surface, and the sealing groove Ⅰ is sealed with a high-temperature-resistant silicone rubber strip; the mold is also divided into two parts, the upper part 1 and the lower part 2, which are connected as one by bolts Ⅱ3; the upper part 1 and the lower part The surface roughness of the contact surface of 2 is 1.6, and the corresponding sealing groove II7 is opened on the contact surface. The sealing groove II7 has a built-in high-temperature resistant silicone rubber strip for sealing; a positioning connection part 6 is set outside the sealing groove II7, and the The positioning connection part 6 includes a left half-shell connection part and a right half-sh...
PUM
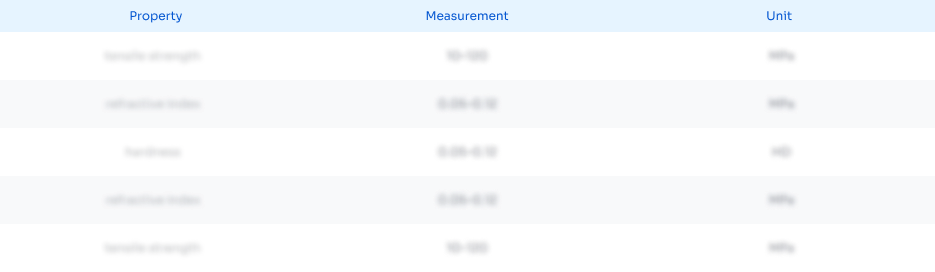
Abstract
Description
Claims
Application Information

- Generate Ideas
- Intellectual Property
- Life Sciences
- Materials
- Tech Scout
- Unparalleled Data Quality
- Higher Quality Content
- 60% Fewer Hallucinations
Browse by: Latest US Patents, China's latest patents, Technical Efficacy Thesaurus, Application Domain, Technology Topic, Popular Technical Reports.
© 2025 PatSnap. All rights reserved.Legal|Privacy policy|Modern Slavery Act Transparency Statement|Sitemap|About US| Contact US: help@patsnap.com