Preparation method of anti-shrinkage autoclaved aerated concrete block dry powder masonry mortar
A technology of concrete blocks and autoclaved gas filling, which is applied in the field of building materials, can solve problems such as plaster layer falling off, affecting the quality of new wall materials to promote construction projects, wall deformation and cracking, etc., to improve adhesion and water retention performance, prevent wall leakage, and solve the effect of cracks
- Summary
- Abstract
- Description
- Claims
- Application Information
AI Technical Summary
Problems solved by technology
Method used
Examples
Embodiment 2
[0016] Embodiment 2 of the present invention includes gypsum, Portland cement, lime powder, dry sand, dispersible latex powder, cellulose ether, calcium formate; its quantitative ratio is 16% of anhydrous gypsum, 35% of Portland cement , lime powder 7.5%, dry sand (20-40 mesh) 40%, dispersible latex powder 0.6%, cellulose ether 0.4%, calcium formate 0.5%.
Embodiment 3
[0018] Embodiment 3 of the present invention includes gypsum, Portland cement, lime powder, dry sand, dispersible latex powder, cellulose ether, calcium formate; its quantity proportion is 20% of anhydrite, 30% of Portland cement , lime powder 13.2%, dry sand (20-40 mesh) 35%, dispersible latex powder 0.8%, cellulose ether 0.4%, calcium formate 0.6%.
Embodiment 4
[0020] Embodiment 4 of the present invention includes gypsum, Portland cement, lime powder, dry sand, dispersible latex powder, cellulose ether, calcium formate; its quantitative ratio is 17% of anhydrite, 30% of Portland cement , lime powder 11.5%, dry sand (20-40 mesh) 40%, dispersible latex powder 0.6%, cellulose ether 0.4%, calcium formate 0.5%.
PUM
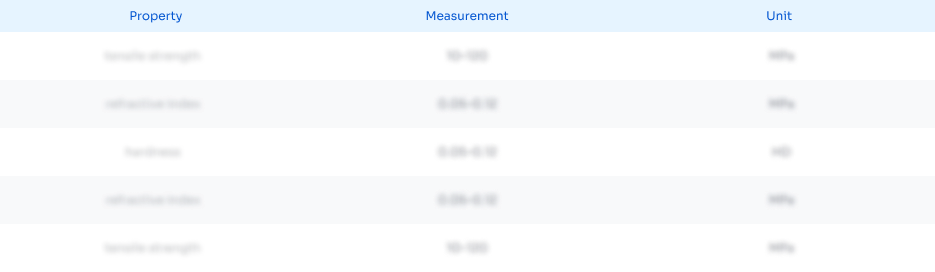
Abstract
Description
Claims
Application Information

- Generate Ideas
- Intellectual Property
- Life Sciences
- Materials
- Tech Scout
- Unparalleled Data Quality
- Higher Quality Content
- 60% Fewer Hallucinations
Browse by: Latest US Patents, China's latest patents, Technical Efficacy Thesaurus, Application Domain, Technology Topic, Popular Technical Reports.
© 2025 PatSnap. All rights reserved.Legal|Privacy policy|Modern Slavery Act Transparency Statement|Sitemap|About US| Contact US: help@patsnap.com