Waste gas purifying method for textile printing and dyeing setting machine and complete equipment thereof
A waste gas purification, textile printing and dyeing technology, applied in the direction of chemical instruments and methods, combined devices, separation methods, etc., can solve the problems of not being able to make full use of the heat energy of high-temperature gas, not being able to meet the needs of environmental protection, and not being able to achieve complete separation, so as to avoid The effect of secondary pollution and tertiary pollution, high efficiency of dust removal and oil collection, and small footprint
- Summary
- Abstract
- Description
- Claims
- Application Information
AI Technical Summary
Problems solved by technology
Method used
Image
Examples
Embodiment Construction
[0027] Such as figure 1 As shown, the present invention is mainly composed of a lint detachment device 1, a heat recovery device 2, an oil-gas separation device 3 and a gas purification device 4 connected in series through a connecting pipe, and between the lint detachment device 1 and the heat recovery device 2 Safety fire doors 5 are provided.
[0028] Its working principle is: after the lint in the exhaust gas is separated from the lint by the lint detachment device 1, after the heat energy recovery by the heat energy recovery device 2 and the oil removal by the oil-gas separation device 3, it will be purified by the gas purification device 4 and then discharged. If accidental flame occurs, the gas passage leading to the heat energy recovery device 2 is closed by the safety fire door 5 .
[0029] Such as figure 2 As shown, the lint removal device 1 is respectively provided with an air inlet 1-2 and an air outlet 1-3 at the left and right ends of the device housing 1-1, a...
PUM
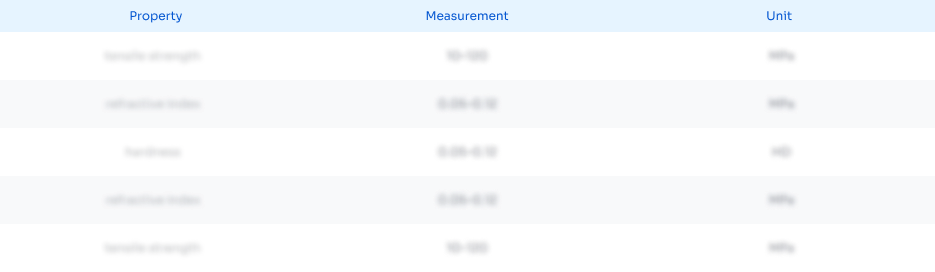
Abstract
Description
Claims
Application Information

- Generate Ideas
- Intellectual Property
- Life Sciences
- Materials
- Tech Scout
- Unparalleled Data Quality
- Higher Quality Content
- 60% Fewer Hallucinations
Browse by: Latest US Patents, China's latest patents, Technical Efficacy Thesaurus, Application Domain, Technology Topic, Popular Technical Reports.
© 2025 PatSnap. All rights reserved.Legal|Privacy policy|Modern Slavery Act Transparency Statement|Sitemap|About US| Contact US: help@patsnap.com