Manufacturing method of one-net multi-mesh nickel screen roller
A manufacturing method and technology of nickel mesh, applied in the field of printing and dyeing rolls, can solve the problems of inability to present a three-dimensional effect, singleness, etc.
- Summary
- Abstract
- Description
- Claims
- Application Information
AI Technical Summary
Problems solved by technology
Method used
Image
Examples
Embodiment Construction
[0017] The mother roller plate of the present invention is 1800 millimeters long, and the diameter is 203.20 millimeters, and the manufacture method of the present invention is further described below.
[0018] Machining, mother roll processing length is 1750mm, diameter is 203.20mm.
[0019] For copper plating, the surface of the mother roll is first plated with 1 wire of bottom nickel, and then 30 wires of copper are plated on one side.
[0020] Grinding, grinding until the diameter of the plate roll is 203.80mm, and polishing to a mirror surface.
[0021] Glue coating, glue coating on the squeegee machine, the workshop temperature is 18 to 25 ° C, the humidity is above 60%, the black glue viscosity is 18 seconds, the scraping speed is 25 Hz, the thickness of the glue layer is 3 to 5 microns, and the plate is evenly coated on the roller A layer of vinyl.
[0022] Pattern making, through computer software, make 3 mesh patterns with different gray levels.
[0023] Laser eng...
PUM
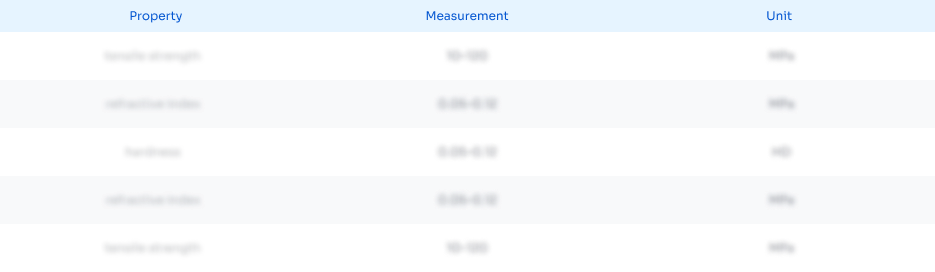
Abstract
Description
Claims
Application Information

- Generate Ideas
- Intellectual Property
- Life Sciences
- Materials
- Tech Scout
- Unparalleled Data Quality
- Higher Quality Content
- 60% Fewer Hallucinations
Browse by: Latest US Patents, China's latest patents, Technical Efficacy Thesaurus, Application Domain, Technology Topic, Popular Technical Reports.
© 2025 PatSnap. All rights reserved.Legal|Privacy policy|Modern Slavery Act Transparency Statement|Sitemap|About US| Contact US: help@patsnap.com