Double-omega-shaped carbon fiber composite material expansion arm and stretching method thereof
A composite material and extending arm technology, which is used in space navigation equipment, space navigation equipment, transportation and packaging, etc., can solve the problem of relying on system reliability and structural air tightness, large reaction impact force of the main satellite, and reduced bending stiffness. and other problems, to achieve the effects of stable deployment process, small reaction impact force of the main satellite, and high bending stiffness
- Summary
- Abstract
- Description
- Claims
- Application Information
AI Technical Summary
Problems solved by technology
Method used
Image
Examples
specific Embodiment approach 1
[0024] Specific implementation mode one: as Figure 1-7 As shown, the double Ω-shaped carbon fiber composite extension arm described in this embodiment includes an extension arm cylinder 1 and a flange end 2, the extension arm cylinder 1 is a carbon fiber composite material cylinder, and the extension arm cylinder 1 is made of two Ω-shaped thin-walled shells 1-1 butt-bonded, and the joints of the extension arm cylinder 1 are respectively formed with two ears 1-2, two ears 1-2 Set opposite to and located on the outer wall of the extension arm cylinder body 1 , the flange end 2 is inserted into one end of the extension arm cylinder body 1 .
specific Embodiment approach 2
[0025] Specific implementation mode two: as Figure 1-7 As shown, the specific process of the deployment method described in this embodiment is:
[0026] Step 1. Through-holes 1-2-1 are evenly distributed along the length direction of the ears 1-2 on both sides of the extension arm cylinder 1;
[0027] Step 2: Fix the other end of the extension arm cylinder 1 on the roller 3, and then wind the extension arm cylinder 1 on the roller 3; the roller 3 with a hollow structure can further reduce the mass;
[0028] Step 3. Install the transmission mechanism with two sprockets 4 at a suitable position below the extension arm cylinder 1, so that the ears on both sides of the extension arm cylinder 1 are meshed with a sprocket 4 at the corresponding position;
[0029] Step 4, set the guide sleeve 5 so that the transmission mechanism with two sprockets 4 is located between the roller 3 and the guide sleeve 5, and one end of the extension arm cylinder 1 passes through the guide sleeve 5;...
specific Embodiment approach 3
[0032] Specific implementation mode three: as figure 1 As shown, in step 2 of this embodiment, the other end of the extension arm cylinder 1 is flattened along the plane where the ear 1-2 is located, and then fixed on the outer wall of the drum 3 by a fixing member. This connection mode has a small volume in a folded state, and can improve the folding (folding) efficiency of the extension arm cylinder body 1 . Other steps are the same as in the second embodiment.
PUM
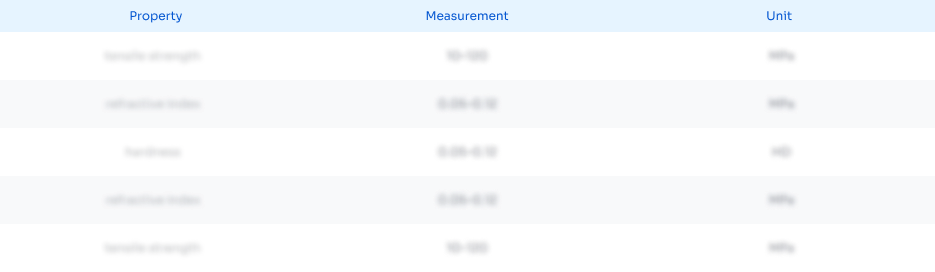
Abstract
Description
Claims
Application Information

- Generate Ideas
- Intellectual Property
- Life Sciences
- Materials
- Tech Scout
- Unparalleled Data Quality
- Higher Quality Content
- 60% Fewer Hallucinations
Browse by: Latest US Patents, China's latest patents, Technical Efficacy Thesaurus, Application Domain, Technology Topic, Popular Technical Reports.
© 2025 PatSnap. All rights reserved.Legal|Privacy policy|Modern Slavery Act Transparency Statement|Sitemap|About US| Contact US: help@patsnap.com