Method for shaping automobile shell in one step
A technology for automobiles and shells, which is applied in the field of one-time forming automobile shells, which can solve problems such as cumbersome production and assembly processes, complex product structures, and low production efficiency, and achieve improved overall strength, impact resistance, and anti-collision performance. , simplify the structure and production process, and reduce the production cost
- Summary
- Abstract
- Description
- Claims
- Application Information
AI Technical Summary
Problems solved by technology
Method used
Examples
Embodiment Construction
[0012] Taking an ordinary car as an example, according to the method for one-shot molding of an automobile body provided by the present invention, the method comprises the following steps: (1) making a pair of car body molds comprising a vehicle body, a chassis and a body cover; (2) making Pull various cores such as car doors, windows, lamps, etc., and insert all kinds of cores into the corresponding core-pulling holes on the car shell mold; (3) Add powdered plastic to the car shell mold and close the mold; ( 4) Turn the car body mold into the heating chamber and make it rotate and heat continuously along the main shaft and the auxiliary shaft perpendicular to each other. The powdery plastic in the car body mold is gradually and evenly coated under the action of gravity and heat energy. Melt and adhere to the entire surface of the mold cavity; (5) transfer the car shell mold to a water mist cooling chamber for water mist cooling; (6) transfer the car shell mold to an air-filled...
PUM
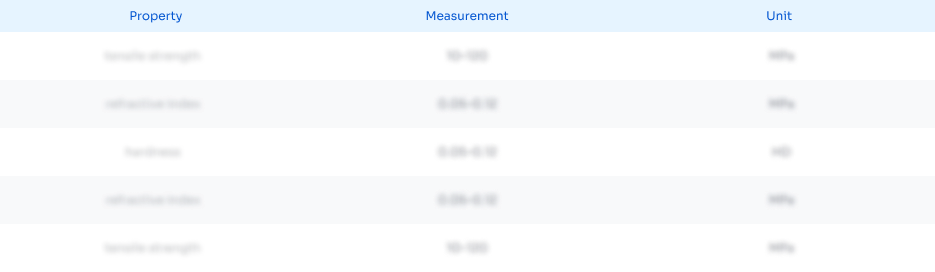
Abstract
Description
Claims
Application Information

- Generate Ideas
- Intellectual Property
- Life Sciences
- Materials
- Tech Scout
- Unparalleled Data Quality
- Higher Quality Content
- 60% Fewer Hallucinations
Browse by: Latest US Patents, China's latest patents, Technical Efficacy Thesaurus, Application Domain, Technology Topic, Popular Technical Reports.
© 2025 PatSnap. All rights reserved.Legal|Privacy policy|Modern Slavery Act Transparency Statement|Sitemap|About US| Contact US: help@patsnap.com