Method for adding nitrogen into stainless steel used for thermonuclear fusion reactor
A thermonuclear fusion and stainless steel technology, which is applied in the field of nitrogen addition of stainless steel, can solve the problems of high inclusion content in molten steel and difficulty in controlling nitrogen content within the target range, and achieve the effect of avoiding high inclusion content in molten steel
- Summary
- Abstract
- Description
- Claims
- Application Information
AI Technical Summary
Problems solved by technology
Method used
Examples
Embodiment 1
[0034] The stainless steel grade of the present embodiment is 316LN, and the mass percent requirement of its composition is:
[0035] 0
[0036] The steps of this embodiment are as follows:
[0037] It is smelted and produced by 18-ton AOD furnace and 18-ton LF furnace.
[0038] 17.32 tons of electric furnace molten steel is blended into the AOD furnace, and the composition of the electric furnace molten steel is as follows (weight percentage):
[0039] C: 1.49% Si: 0.13% Mn: 0.45% P: 0.016% S: 0.003%
[0040] Cr: 15.71% Ni: 12.93% Mo: 2.15% N: 0.03% Co: 0.03%
[0041] Nb: 0.01% Ta: 0.01%
[0042] The rest is Fe and unavoidable impurities.
[0043] The AOD furnace operates as follows:
[0044] Time Operation content
[0045] 17:45 After adding steel, blow gas O on the botto...
example 2
[0070] The stainless steel grade of this embodiment is 316L(N)-IG. The mass percentage requirements of its ingredients are;
[0071] 0
[0072] The steps of this embodiment are as follows:
[0073] It is smelted and produced by 18-ton AOD furnace and 18-ton LF furnace.
[0074] 17.32 tons of electric furnace molten steel is blended into the AOD furnace, and the composition of the electric furnace molten steel is as follows (weight percentage):
[0075] C: 1.52% Si: 0.23% Mn: 0.77% P: 0.017% S: 0.003%
[0076] Cr: 16.33% Ni: 13.08% Mo: 2.15% N: 300ppm The remainder is Fe and unavoidable impurities.
[0077] The AOD furnace operates as follows:
[0078] Time Operation content
[0079] 3:15 After mixing steel, blow O on the bottom side 2 :N 2 =0:400m 3 / h, temperature measur...
PUM
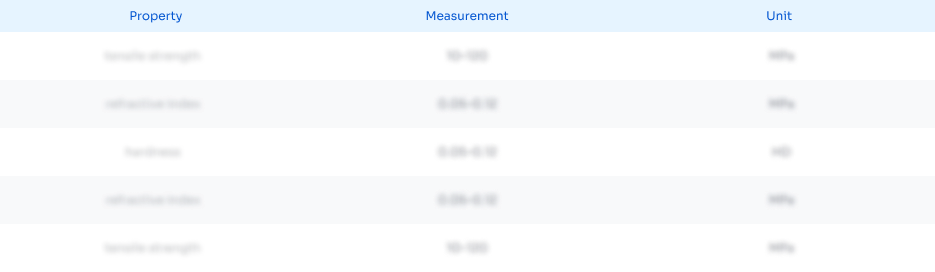
Abstract
Description
Claims
Application Information

- R&D
- Intellectual Property
- Life Sciences
- Materials
- Tech Scout
- Unparalleled Data Quality
- Higher Quality Content
- 60% Fewer Hallucinations
Browse by: Latest US Patents, China's latest patents, Technical Efficacy Thesaurus, Application Domain, Technology Topic, Popular Technical Reports.
© 2025 PatSnap. All rights reserved.Legal|Privacy policy|Modern Slavery Act Transparency Statement|Sitemap|About US| Contact US: help@patsnap.com