Dephosphorization method of high-phosphorous chromium-nickel pig iron
A technology of nickel pig iron and high phosphorus chromium is applied in the field of high phosphorus chromium nickel pig iron dephosphorization, which can solve the problems of short time, high cost and long time, and achieve the effects of short time, low cost and improved efficiency.
- Summary
- Abstract
- Description
- Claims
- Application Information
AI Technical Summary
Problems solved by technology
Method used
Examples
Embodiment 1
[0024] This embodiment is the following sequential steps:
[0025] I EAF preliminary desilication
[0026] Add 75.2t of high-phosphorus-chromium-nickel pig iron with the following weight percentages into the electric arc furnace for melting and preliminary desiliconization:
[0027] C: 4.0%; Si: 2.55%; Mn: 0.70%; P: 0.061%; S: 0.081%;
[0028] Cr: 3.00%; Ni: 4.45%; the rest is Fe and unavoidable impurities.
[0029] Add lime 3300kg in three batches, oxygen blowing volume 50Nm 3 / per minute, after 90 minutes of smelting, (C, Si, Mn are oxidized during the desiliconization process), the weight percentage of the composition of the molten iron before tapping the electric furnace is: C: 2.34%; Si: 0.09%; Mn: 0.20 %; P: 0.073%; S: 0.069%; Cr: 3.36%; Ni: 4.75%; the rest is Fe and unavoidable impurities.
[0030] The tapping temperature of the electric furnace is 1643°C.
[0031] II Remove the slag from the electric furnace and add it to the AOD furnace
[0032] After removing ...
Embodiment 2
[0042] This embodiment is the following sequential steps:
[0043] I EAF preliminary desilication
[0044] Add 75.4t of high-phosphorus chromium-nickel pig iron with the following weight percentages into the electric arc furnace for melting and preliminary desiliconization:
[0045] C: 4.0%; Si: 2.55%; Mn: 0.70%; P: 0.061%; S: 0.081%;
[0046] Cr: 3.00%; Ni: 4.8%; the rest is Fe and unavoidable impurities.
[0047] Add lime 3300kg in three batches, oxygen blowing volume 50Nm 3 / per minute, after 90 minutes of smelting, (C, Si, Mn are oxidized during the desiliconization process), the weight percentage of the composition of the molten iron before tapping the electric furnace is: C: 2.34%; Si: 0.05%; Mn: 0.25 %; P: 0.051%; S: 0.069%; Cr: 3.36%; Ni: 4.75%; the rest is Fe and unavoidable impurities.
[0048] The tapping temperature of the electric furnace is 1637°C.
[0049] II Remove the slag from the electric furnace and add it to the AOD furnace
[0050] After removing t...
Embodiment 3
[0060] This embodiment is the following sequential steps:
[0061] I EAF preliminary desilication
[0062] Add 74.4t of high-phosphorus-chromium-nickel pig iron with the following weight percentages into the electric arc furnace for melting and preliminary desiliconization:
[0063] C: 4.0%; Si: 2.45%; Mn: 0.70%; P: 0.061%; S: 0.081%;
[0064] Cr: 3.00%; Ni: 5.8%; the rest is Fe and unavoidable impurities.
[0065] Add lime 3300kg in three batches, oxygen blowing volume N50m 3 / per minute, after 90 minutes of smelting, (C, Si, Mn are oxidized during the desiliconization process), the weight percentage of the molten iron before tapping the electric furnace is: C: 2.58%; Si: 0.26%; Mn: 0.3 %; P: 0.098%; S: 0.067%; Cr: 3.32%; Ni: 6.23%; the rest is Fe and unavoidable impurities.
[0066] The tapping temperature of the electric furnace is 1643°C.
[0067] II Remove the slag from the electric furnace and add it to the AOD furnace
[0068] After removing the slag on the surface...
PUM
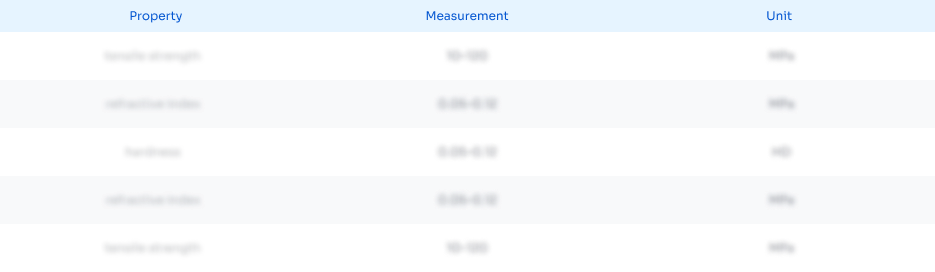
Abstract
Description
Claims
Application Information

- R&D Engineer
- R&D Manager
- IP Professional
- Industry Leading Data Capabilities
- Powerful AI technology
- Patent DNA Extraction
Browse by: Latest US Patents, China's latest patents, Technical Efficacy Thesaurus, Application Domain, Technology Topic, Popular Technical Reports.
© 2024 PatSnap. All rights reserved.Legal|Privacy policy|Modern Slavery Act Transparency Statement|Sitemap|About US| Contact US: help@patsnap.com