Gasoline olefin reducing catalytic cracking method and device
A catalytic cracking device and a catalytic cracking technology are applied in the field of catalytic cracking for reducing gasoline olefins, which can solve the problems of high contact temperature between a regenerated catalyst and raw materials, inability to flexibly control the temperature of the catalyst, and low coking capacity of the device, so as to reduce the catalyst storage capacity. , the effect of size reduction and equipment investment reduction
- Summary
- Abstract
- Description
- Claims
- Application Information
AI Technical Summary
Problems solved by technology
Method used
Image
Examples
Embodiment 1
[0067] The raw material used in the test was atmospheric residual oil from Daqing, and the catalyst was commercially available CC-20 catalytic cracking industrial equilibrium catalyst with a microreactive activity of 65.
[0068] The catalytic cracking program is carried out on a small-scale fluidized bed device in the laboratory. The catalyst to be produced is burnt in a tubular manner and then enters the regenerator with a micro-reaction activity of 65. The stripping medium in the stripping section of the settler is water vapor, and the stripping temperature is 500°C. Table 5 shows the operating conditions, product distribution and properties of some products in the catalytic cracking unit of this example.
Embodiment 2
[0070] According to Example 1, the difference is the temperature of the regenerated catalyst from the regenerator, the reaction temperature of the raw material, the ratio of agent to oil, and the reaction time. The operating conditions, product distribution and some product properties of the catalytic cracking unit in this embodiment are shown in Table 6.
Embodiment 3
[0072] According to embodiment 1, the difference is the temperature of the regenerated catalyst from the regenerator, the agent-oil ratio and the reaction time of the raw materials during the reaction. The operating conditions, product distribution and some product properties of the catalytic cracking unit in this embodiment are shown in Table 7.
PUM
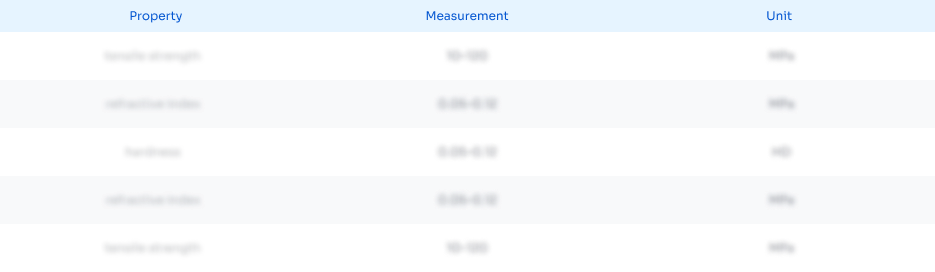
Abstract
Description
Claims
Application Information

- Generate Ideas
- Intellectual Property
- Life Sciences
- Materials
- Tech Scout
- Unparalleled Data Quality
- Higher Quality Content
- 60% Fewer Hallucinations
Browse by: Latest US Patents, China's latest patents, Technical Efficacy Thesaurus, Application Domain, Technology Topic, Popular Technical Reports.
© 2025 PatSnap. All rights reserved.Legal|Privacy policy|Modern Slavery Act Transparency Statement|Sitemap|About US| Contact US: help@patsnap.com