Method of manufacturing multi-layered printed circuit board
A manufacturing method and multi-layer printing technology, applied in multi-layer circuit manufacturing, printed circuit manufacturing, printed circuit, etc., can solve problems such as inability to obtain multi-layer printed wiring boards, difficulty in forming outer layer circuit patterns, etc., and achieve easy electrodeposition Improved performance, reduced plating thickness, finer circuit patterns
- Summary
- Abstract
- Description
- Claims
- Application Information
AI Technical Summary
Problems solved by technology
Method used
Image
Examples
Embodiment Construction
[0057] Hereinafter, the manufacturing method of the build-up type multilayer printed wiring board which has a multilayer via structure concerning embodiment of this invention is demonstrated, referring drawings.
[0058] In addition, the same code|symbol is attached|subjected to the structural element which has an equivalent function, and detailed description is abbreviate|omitted. In addition, the drawings are schematic and are shown centering on the characteristic parts related to the embodiment, and the relationship between the thickness and the plane size, the ratio of the thickness of each layer, and the like are different from the actual ones.
[0059] First, use Figure 1A to Figure 1C and figure 2 Next, a method for manufacturing the build-up type multilayer printed wiring board 32 having the via structure according to the embodiment of the present invention will be described.
[0060] Figure 1A to Figure 1C It is a process sectional drawing for demonstrating the ...
PUM
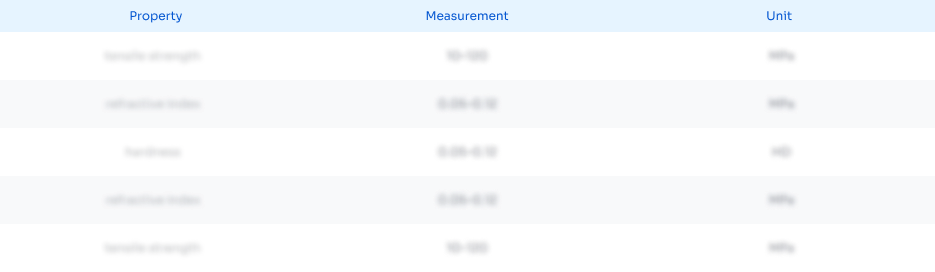
Abstract
Description
Claims
Application Information

- R&D
- Intellectual Property
- Life Sciences
- Materials
- Tech Scout
- Unparalleled Data Quality
- Higher Quality Content
- 60% Fewer Hallucinations
Browse by: Latest US Patents, China's latest patents, Technical Efficacy Thesaurus, Application Domain, Technology Topic, Popular Technical Reports.
© 2025 PatSnap. All rights reserved.Legal|Privacy policy|Modern Slavery Act Transparency Statement|Sitemap|About US| Contact US: help@patsnap.com