Feed line automation system
A feeder automation and feeder technology, which is applied in information technology support systems, electrical components, circuit devices, etc., can solve the problems of high communication reliability requirements, heavy burden on the main station, and slow down the processing speed of failures. And the effect of processing direct and fast, shortening the time of fault processing, reducing communication paralysis
- Summary
- Abstract
- Description
- Claims
- Application Information
AI Technical Summary
Problems solved by technology
Method used
Image
Examples
Embodiment 1
[0030] See figure 1 , the feeder automation system disclosed in the embodiment of the present invention includes a master station system 11 , a point-to-point peer-to-peer communication network 12 and a distribution automation terminal FTU 13 . The master station system 11 is connected to a communication processor (Communication Processor, CP), and the CP is connected to the point-to-point communication network 12; the FTU 13 is connected to the point-to-point communication network 12. The point-to-point peer-to-peer communication network 12 is used to realize peer-to-peer communication between adjacent FTUs 13, and the FTUs 13 are used to perform local fault location, fault isolation and power supply recovery of non-faulty sections, and the CP is used to forward the information of the FTU 13 to the main station 11 data, the data is provided to the staff of the master station as the time processing sequence soe information of the master station 11.
[0031] The system logic s...
Embodiment 2
[0048] See figure 2 , The feeder automation system disclosed in this embodiment includes: a master station system 21 , a peer-to-peer network 22 and a distribution automation terminal FTU 23 . The master station system 21 is connected to a communication processor (Communication Processor, CP), and the CP is connected to the peer-to-peer network 22 ; the FTU 23 is connected to the peer-to-peer network 22 .
[0049] In the system disclosed in this embodiment, the point-to-point peer-to-peer communication network is an optical fiber industrial Ethernet; image 3As shown, the FTU22 is arranged in the ring main unit 31; the switch type of the ring main unit 31 is: the incoming line switch is a circuit breaker, and the outgoing line switch is a load switch. The bus bar of the ring main unit 31 is configured with a single-phase voltage transformer PT, and the incoming and outgoing lines of the ring main unit 31 are configured with a three-phase current transformer CT. Circuit brea...
PUM
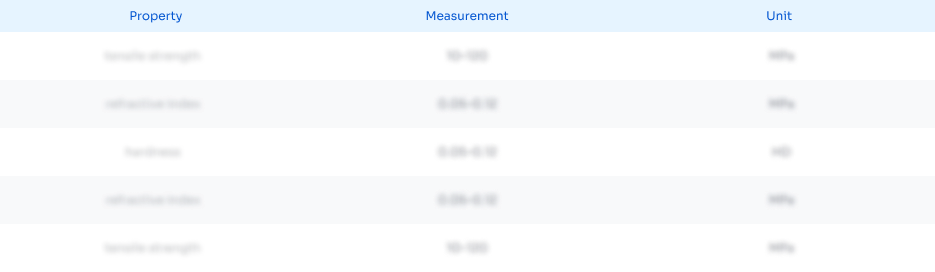
Abstract
Description
Claims
Application Information

- R&D Engineer
- R&D Manager
- IP Professional
- Industry Leading Data Capabilities
- Powerful AI technology
- Patent DNA Extraction
Browse by: Latest US Patents, China's latest patents, Technical Efficacy Thesaurus, Application Domain, Technology Topic, Popular Technical Reports.
© 2024 PatSnap. All rights reserved.Legal|Privacy policy|Modern Slavery Act Transparency Statement|Sitemap|About US| Contact US: help@patsnap.com