Novel MEMS (micro electro mechanical system) centrifugal-type gyroscope
A centrifugal and gyro technology, which is applied in the field of inertial measurement, can solve the problems of high noise of MEMS vibrating gyro, high cost of MEMS rotor gyro, and orthogonal coupling error, etc., so as to improve the stability of zero bias, reduce energy consumption, and improve The effect of precision
- Summary
- Abstract
- Description
- Claims
- Application Information
AI Technical Summary
Problems solved by technology
Method used
Image
Examples
Embodiment 1
[0018] refer to figure 1 , a MEMS centrifugal gyro, comprising a first mass 1, a second mass 2, a third mass 3, a fourth mass 4, a decoupling beam 5, an elastic beam 6, a central anchor point 7, and movable comb teeth 8 and fixed comb teeth 9; the first mass block 1, the second mass block 2, the third mass block 3, and the fourth mass block 4 are evenly distributed around the center anchor point 7 in a ring, the first mass block 1, the second mass block The mass block 2, the third mass block 3, the fourth mass block 4 and the central anchor point 7 are all connected by elastic beams 6; adjacent mass blocks are connected by two parallel arc-shaped decoupling beams 7; the first A set of movable comb teeth 8 are respectively arranged on the mass 1 , the second mass 2 , the third mass 3 and the fourth mass 4 , and form a comb capacitance with the corresponding fixed combs 9 .
[0019] Theoretical analysis of MEMS centrifugal gyroscope in the present embodiment is as follows ima...
Embodiment 2
[0025] refer to figure 2 , the MEMS centrifugal gyro of the present embodiment includes a first mass 1, a second mass 2, a third mass 3, a fourth mass 4, a decoupling beam 5, an elastic beam 6, a central anchor point 7, a movable Comb teeth 8, fixed comb teeth 9 and diagonal anchor points 10; the first mass block 1, the second mass block 2, the third mass block 3, and the fourth mass block 4 are evenly distributed around the center anchor point 7 , the first mass 1, the second mass 2, the third mass 3, the fourth mass 4 and the central anchor point 7 are all connected by elastic beams 6; between two adjacent mass blocks is a diagonal anchor point 10, and each mass is supported and suspended on two adjacent diagonal anchor points 10 by the decoupling beam 5; the first mass 1, the second mass 2, the third mass 3 and the fourth mass A group of movable comb teeth 8 are respectively arranged on the 4, and form a comb tooth capacitor with corresponding fixed comb teeth 9. The dis...
PUM
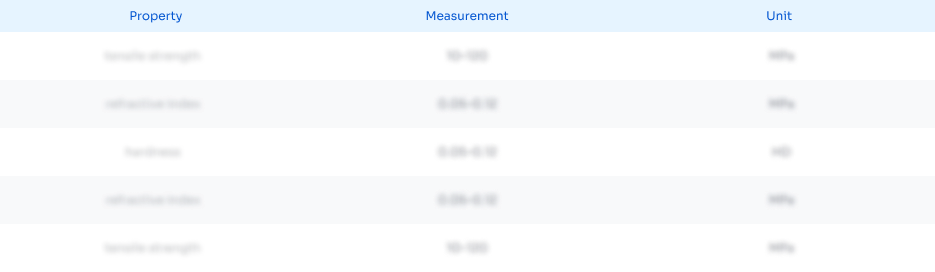
Abstract
Description
Claims
Application Information

- R&D
- Intellectual Property
- Life Sciences
- Materials
- Tech Scout
- Unparalleled Data Quality
- Higher Quality Content
- 60% Fewer Hallucinations
Browse by: Latest US Patents, China's latest patents, Technical Efficacy Thesaurus, Application Domain, Technology Topic, Popular Technical Reports.
© 2025 PatSnap. All rights reserved.Legal|Privacy policy|Modern Slavery Act Transparency Statement|Sitemap|About US| Contact US: help@patsnap.com