Novel MEMS (Micro-electromechanical System) jet rotor gyroscope
A technology of jet rotor and gyroscope, applied in the field of inertial measurement, can solve problems such as low integration, and achieve the effects of ensuring accuracy, high gyro accuracy, and eliminating orthogonal coupling errors.
- Summary
- Abstract
- Description
- Claims
- Application Information
AI Technical Summary
Problems solved by technology
Method used
Image
Examples
Embodiment 1
[0027] refer to figure 1 , figure 2 , image 3 , Figure 4 , Figure 5 , Figure 6 , the MEMS jet rotor gyro of the present embodiment comprises an upper detection layer 36, a cavity layer 35 and a lower detection layer 37 in turn; the cavity layer 35 has a through cylindrical cavity, which is symmetrical on both sides of the cylindrical cavity The first vibrating cavity 28 and the second vibrating cavity 29 are arranged; the first vibrating cavity 28 and the second vibrating cavity 29 do not penetrate the cavity layer 35, and the non-penetrating parts form the first vibrating film 23 and the second vibrating film respectively 24; the cylindrical cavity communicates with the first vibration chamber 28 and the second vibration chamber 29 through the first nozzle 14 and the second nozzle 15 respectively; the first nozzle 14 and the second nozzle 15 are radially staggered; the first vibration The first piezoelectric sheet 19 and the second piezoelectric sheet 20 are respect...
Embodiment 2
[0032] refer to Figure 8 and Figure 9 , the MEMS jet rotor gyroscope of the present embodiment includes an upper detection layer, a cavity layer and a lower detection layer in turn; the cavity layer has a through cylindrical cavity, and first circumferentially evenly distributed around the cylindrical cavity. The vibration cavity 28, the second vibration cavity 29, the third vibration cavity 30 and the fourth vibration cavity 31; the first vibration cavity 28, the second vibration cavity 29, the third vibration cavity 30 and the fourth vibration cavity 31 do not pass through the described Cavity layer 35, the first vibrating film, the second vibrating film, the third vibrating film and the fourth vibrating film are respectively formed in the non-penetrating part; 16. The fourth nozzle 17 communicates with the first vibration chamber 28, the second vibration chamber 29, the third vibration chamber 30 and the fourth vibration chamber 31; the first nozzle 14, the second nozzle...
PUM
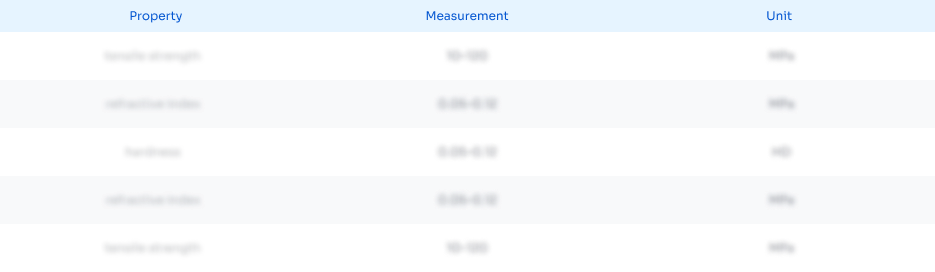
Abstract
Description
Claims
Application Information

- Generate Ideas
- Intellectual Property
- Life Sciences
- Materials
- Tech Scout
- Unparalleled Data Quality
- Higher Quality Content
- 60% Fewer Hallucinations
Browse by: Latest US Patents, China's latest patents, Technical Efficacy Thesaurus, Application Domain, Technology Topic, Popular Technical Reports.
© 2025 PatSnap. All rights reserved.Legal|Privacy policy|Modern Slavery Act Transparency Statement|Sitemap|About US| Contact US: help@patsnap.com