On-line monitoring device for tool wear of shield machine based on resistance row
A shield machine tool and monitoring device technology, applied in measuring devices, using electrical devices, using electromagnetic means, etc., can solve problems such as difficult maintenance, inability to realize continuous monitoring, and high wiring requirements, so as to ensure reliability and avoid economic losses and personal injury, prolonging the effect of safety life
- Summary
- Abstract
- Description
- Claims
- Application Information
AI Technical Summary
Problems solved by technology
Method used
Image
Examples
Embodiment Construction
[0016] The structure of the present invention will be further described below in conjunction with the accompanying drawings and through specific embodiments. It should be noted that this embodiment is descriptive rather than restrictive, and should not limit the protection scope of the present invention.
[0017] The online monitoring device for shield machine tool wear based on the resistance row type is composed of a resistance row 1, a resistance row base 2 and a resistance lead plug 3 to form a resistance row tool wear sensor ( figure 1 ). The resistor row sensor is embedded in the tool 4 of the shield machine, the part where the resistor row contacts the tool is filled with epoxy resin, the part where the resistor row base 2 contacts the tool is provided with a rubber pad 5, and the resistor row base 2 passes through the lock nut 6 is fixed with the tool as a whole ( figure 2 ). A signal amplifier 8 is provided on the cutterhead 7, a transmitting antenna 9 is arranged...
PUM
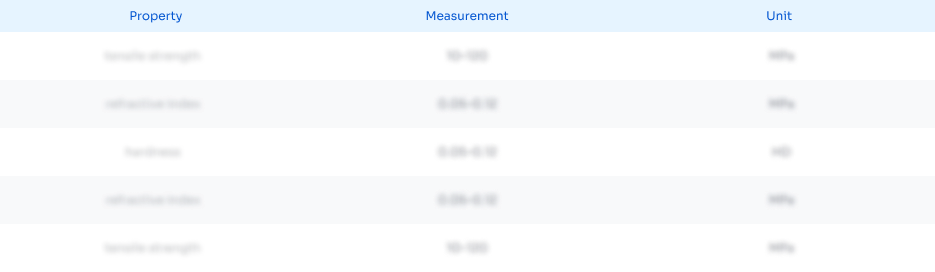
Abstract
Description
Claims
Application Information

- R&D
- Intellectual Property
- Life Sciences
- Materials
- Tech Scout
- Unparalleled Data Quality
- Higher Quality Content
- 60% Fewer Hallucinations
Browse by: Latest US Patents, China's latest patents, Technical Efficacy Thesaurus, Application Domain, Technology Topic, Popular Technical Reports.
© 2025 PatSnap. All rights reserved.Legal|Privacy policy|Modern Slavery Act Transparency Statement|Sitemap|About US| Contact US: help@patsnap.com