Control system for remote working machines
一种控制系统、工作机的技术,应用在控制/调节系统、机械控制装置、备有多个被控构件的控制机构等方向,能够解决慢效率、不能同时操作等问题
- Summary
- Abstract
- Description
- Claims
- Application Information
AI Technical Summary
Problems solved by technology
Method used
Image
Examples
Embodiment Construction
[0017] Reference figure 1 , Shows the working machine 10. It is a demolition robot that is driven by electricity and has a power cable 8. In the figure, the cable 8 is shown in a separated state, but in fact it is connected to the cable leading to the socket and usually has a high voltage current. The working machine is driven by crawlers 6 and has a rotating tower 7. Arm consisting of several parts (refer to figure 2 Described in more detail) fixed to the tower. No removal tool is installed on the arm. The working machine has four supporting legs 5, in this case all supporting legs are raised. The operator uses the remote controller 11 to operate the working machine, in this case the remote controller is put on the operator's shoulder. However, the remote control can of course also be fixed in a different way (for example, by a belt). The remote controller has a left control lever 12 and a right control lever 13.
[0018] figure 2 The demolition machine is shown in more ...
PUM
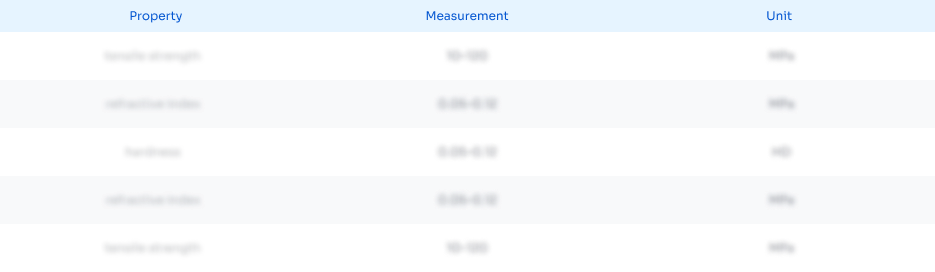
Abstract
Description
Claims
Application Information

- R&D
- Intellectual Property
- Life Sciences
- Materials
- Tech Scout
- Unparalleled Data Quality
- Higher Quality Content
- 60% Fewer Hallucinations
Browse by: Latest US Patents, China's latest patents, Technical Efficacy Thesaurus, Application Domain, Technology Topic, Popular Technical Reports.
© 2025 PatSnap. All rights reserved.Legal|Privacy policy|Modern Slavery Act Transparency Statement|Sitemap|About US| Contact US: help@patsnap.com