Structural Design Method for Shock-resistant Protective Shell of Test Equipment
A technology of structural design and protective shell, which is applied in the direction of the measuring device shell, etc., can solve the problems of unfavorable design method of impact protection structure, increased design cost, and prolonged design cycle of test equipment, so as to improve the design cycle and reliability, improve Reliability, the effect of improving the design cycle
- Summary
- Abstract
- Description
- Claims
- Application Information
AI Technical Summary
Problems solved by technology
Method used
Image
Examples
Embodiment Construction
[0013] The method for designing the structure of the impact-resistant protective shell of the test equipment is realized by the following steps:
[0014] 1) Design and determine the shape and structure of the impact-resistant shell: the shape of the impact-resistant shell adopts the double-layer protective structure of the outer cylindrical shell and the inner cylindrical shell; according to the actual impact force requirements, combined with the inner cylindrical shell The relationship between the radius and the radius of the outer cylindrical shell determines the width of the annular gap between the inner cylindrical shell and the outer cylindrical shell; in the annular gap between the inner cylindrical shell and the outer cylindrical shell Add buffer material, and encapsulate the circuit board through the inner cavity of the inner cylindrical shell with potting material;
[0015] In the step 1), considering that the impact resistance of the cylindrical structure in nature i...
PUM
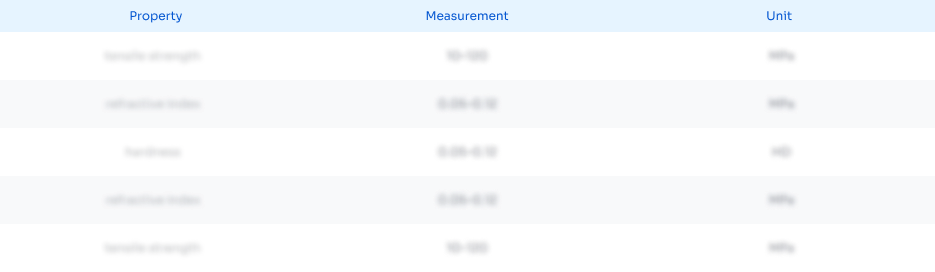
Abstract
Description
Claims
Application Information

- Generate Ideas
- Intellectual Property
- Life Sciences
- Materials
- Tech Scout
- Unparalleled Data Quality
- Higher Quality Content
- 60% Fewer Hallucinations
Browse by: Latest US Patents, China's latest patents, Technical Efficacy Thesaurus, Application Domain, Technology Topic, Popular Technical Reports.
© 2025 PatSnap. All rights reserved.Legal|Privacy policy|Modern Slavery Act Transparency Statement|Sitemap|About US| Contact US: help@patsnap.com