Method for preparing metal micro-nano hollow spherical powder
A powder preparation, micro-nano technology, applied in the fields of nanotechnology, nanotechnology, nanotechnology for materials and surface science, etc., can solve the problems of ungiven shell thickness, high processing conditions, and complex device structure, etc. Achieve the effect of shortening the production cycle, shortening the production cycle, and simple processing conditions
- Summary
- Abstract
- Description
- Claims
- Application Information
AI Technical Summary
Problems solved by technology
Method used
Image
Examples
Embodiment 1
[0035] The metal nickel plate is processed into a rectangular tool electrode 3 and a workpiece electrode 6, and the electrode surface is deoxidized and smoothed. The workpiece electrode as the negative electrode is placed at the bottom of the cylindrical working fluid tank 8, and the tool electrode as the positive electrode is suspended in the working fluid tank through the servo feed device 2 fixed on the wall of the working fluid tank, pointing downward. Facing the workpiece electrode, in order to maintain the required gap for spark discharge during processing, connect the tool electrode and workpiece electrode to the positive and negative interfaces of the pulse power supply device 1, pour kerosene as the working fluid 4 into the working fluid tank, and make the tool electrode The lower end of the part extends into the kerosene. The power of the ultrasonic generator of the ultrasonic device is 100W, and the frequency is 20KHZ. There are 6 ultrasonic vibrators in the ultraso...
Embodiment 2
[0038] The metal nickel plate is processed into a rectangular tool electrode 3 and a workpiece electrode 6, and the electrode surface is deoxidized and smoothed. The workpiece electrode as a negative electrode is placed at the bottom of the square working fluid tank 8, and the tool electrode as a positive electrode is suspended in the working fluid tank through the servo feed device 2 fixed on the wall of the working fluid tank, pointing downwards to the working fluid tank. In order to maintain the required gap for spark discharge during processing, connect the tool electrode and the workpiece electrode with the positive and negative interfaces of the pulse power supply device 1, and pour the plasma water as the working fluid 4 into the working fluid tank to make the tool electrode The lower part protrudes into the plasma water. The power of the ultrasonic generator of the ultrasonic device is 200W, and the frequency is 60KHZ. There are 4 ultrasonic vibrators in the ultrasonic...
Embodiment 3
[0041] The metal copper plate is processed into rectangular tool electrode 3 and workpiece electrode 6, and the electrode surface is deoxidized and smoothed. The workpiece electrode as the negative electrode is placed at the bottom of the cylindrical working fluid tank 8, and the tool electrode as the positive electrode is suspended in the working fluid tank through the servo feed device 2 fixed on the wall of the working fluid tank, pointing downward. Facing the workpiece electrode, in order to maintain the required gap for spark discharge during processing, connect the tool electrode and workpiece electrode to the positive and negative interfaces of the pulse power supply device 1, pour kerosene as the working fluid 4 into the working fluid tank, and make the tool electrode The lower end of the part extends into the kerosene. The power of the ultrasonic generator of the ultrasonic device is 400W, and the frequency is 100KHZ. There are 2 ultrasonic vibrators in the ultrasonic...
PUM
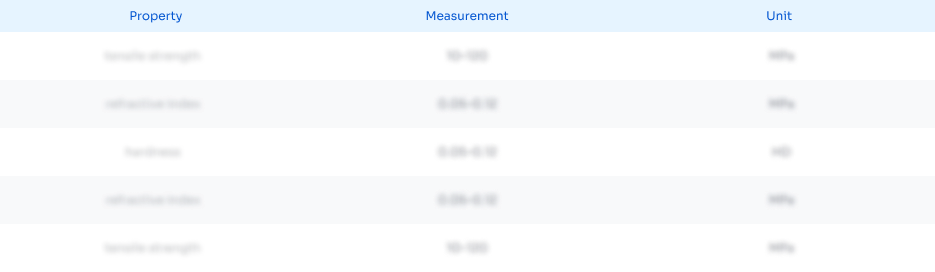
Abstract
Description
Claims
Application Information

- R&D Engineer
- R&D Manager
- IP Professional
- Industry Leading Data Capabilities
- Powerful AI technology
- Patent DNA Extraction
Browse by: Latest US Patents, China's latest patents, Technical Efficacy Thesaurus, Application Domain, Technology Topic, Popular Technical Reports.
© 2024 PatSnap. All rights reserved.Legal|Privacy policy|Modern Slavery Act Transparency Statement|Sitemap|About US| Contact US: help@patsnap.com