Integrated board production method
A production method and integrated board technology are applied in the field of sheet metal processing to achieve the effects of improving economic benefits, good static bending strength and elastic modulus, and reducing production costs
- Summary
- Abstract
- Description
- Claims
- Application Information
AI Technical Summary
Problems solved by technology
Method used
Image
Examples
Embodiment 1
[0043] Embodiment 1: a kind of integrated board production method, it comprises the following steps successively:
[0044] (1) Material selection: The leftovers and secondary materials produced in the rotary cutting of Maras and / or mahogany and / or eucalyptus and / or poplar, the leftovers and plant straws produced in the process of bamboo product processing are used as raw materials;
[0045] (2) Drying: Put the raw materials in a natural drying place first, and when the moisture content is below 35%, they are sent to the drying kiln for forced drying. The humidity in the drying kiln is controlled at 70%, and the time is 2 days. The temperature of the day is 50°C, and maintain a daily temperature increase rate of 20°C until the temperature reaches 90°C, reducing the moisture content to 9%;
[0046] (3) Dipping: use phenolic glue for dipping, and the amount of sizing is 200g / m 2 , the dipping time is 30min;
[0047] (4) Re-drying: Put the dipped raw materials into the temperatu...
Embodiment 2
[0063] Embodiment 2: Embodiment 1: a kind of integrated board production method, it comprises the following steps successively:
[0064] (1) Material selection: The leftovers and secondary materials produced in the rotary cutting of Maras and / or mahogany and / or eucalyptus and / or poplar, the leftovers and plant straws produced in the process of bamboo product processing are used as raw materials;
[0065] (2) Drying: first place the raw materials in a natural drying place, and when they are air-dried to a moisture content below 35%, they are sent to a drying kiln for forced drying. The humidity in the drying kiln is controlled at 80% for 2 days. The temperature of the day is 60°C, and maintain a daily temperature rise rate of 20°C until the temperature reaches 100°C, reducing the moisture content to 10%;
[0066] (3) Dipping: use phenolic glue for dipping, and the amount of sizing is 260g / m 2 , the dipping time is 70min;
[0067] (4) Re-drying: Put the dipped raw materials in...
Embodiment 3
[0083] Embodiment 3: Embodiment 1: a kind of integrated board production method, it comprises the following steps successively:
[0084] (1) Material selection: The leftovers and secondary materials produced in the rotary cutting of Maras and / or mahogany and / or eucalyptus and / or poplar, the leftovers and plant straws produced in the process of bamboo product processing are used as raw materials;
[0085] (2) Drying: first place the raw materials in a natural drying place, and when the moisture content is below 35%, they are sent to the drying kiln for forced drying. The humidity in the drying kiln is controlled at 90%, and the time is 2 days. The temperature of the day is 60°C, and maintain a daily temperature increase rate of 20°C until the temperature reaches 100°C, reducing the moisture content to 11%;
[0086] (3) Dipping: use phenolic glue for dipping, and the amount of sizing is 300g / m 2 , the dipping time is 90min;
[0087] (4) Re-drying: Put the dipped raw materials ...
PUM
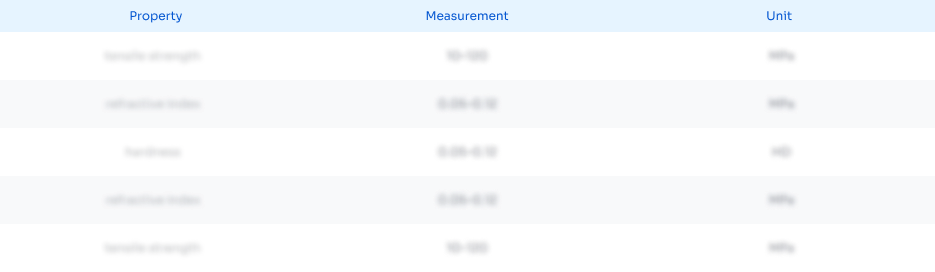
Abstract
Description
Claims
Application Information

- R&D
- Intellectual Property
- Life Sciences
- Materials
- Tech Scout
- Unparalleled Data Quality
- Higher Quality Content
- 60% Fewer Hallucinations
Browse by: Latest US Patents, China's latest patents, Technical Efficacy Thesaurus, Application Domain, Technology Topic, Popular Technical Reports.
© 2025 PatSnap. All rights reserved.Legal|Privacy policy|Modern Slavery Act Transparency Statement|Sitemap|About US| Contact US: help@patsnap.com