Coreless permanent magnet linear motor with cooling structure, manufacturing mould for winding coil thereof and machining process for winding coil
A permanent magnet linear motor and cooling structure technology, applied in the direction of electric components, manufacturing motor generators, magnetic circuit shape/style/structure, etc., to achieve the effect of simple structure, easy manufacture, neat and beautiful appearance
- Summary
- Abstract
- Description
- Claims
- Application Information
AI Technical Summary
Problems solved by technology
Method used
Image
Examples
specific Embodiment approach 1
[0031] Specific implementation mode one: the following combination Figure 1 to Figure 5 Describe this embodiment. This embodiment includes a stator with a double-sided structure and a mover 2. The stator is arranged on both sides of the mover 2 in mirror image symmetry. The stator includes a stator yoke 1-1 and NS-level permanent magnets 1-2 staggered. , an air gap is formed between the stator and the mover 2,
[0032] The mover 2 includes an armature winding 2-1 and a cooling pipeline 2-2. The armature winding 2-1 is a double-layer non-overlapping fractional slot concentrated winding. The upper end and the lower end of the armature winding 2-1 are arc-shaped. The upper end and the lower end of the armature winding 2-1 are formed with arc-shaped through holes along the moving direction, and the cross section of the armature winding 2-1 is I-shaped along the direction perpendicular to the moving direction.
[0033] The cooling pipeline 2-2 is composed of an upper pipeline 2-2...
specific Embodiment approach 2
[0040] Specific implementation mode two: the following combination Figure 3 to Figure 5 This embodiment is described. This embodiment is a further description of Embodiment 1. Both the upper pipeline 2-21 and the lower pipeline 2-22 in this embodiment are in close contact with the inner surface of the end of the armature winding 2-1. catch.
specific Embodiment approach 3
[0041] Embodiment 3: This embodiment is a further description of Embodiment 1 or 2, and the span of the armature winding 2-1 is one virtual slot.
PUM
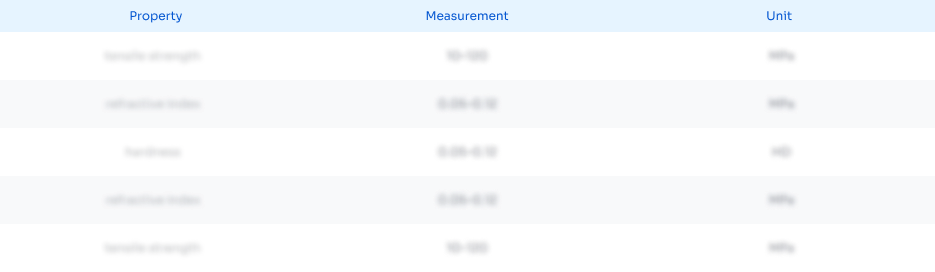
Abstract
Description
Claims
Application Information

- Generate Ideas
- Intellectual Property
- Life Sciences
- Materials
- Tech Scout
- Unparalleled Data Quality
- Higher Quality Content
- 60% Fewer Hallucinations
Browse by: Latest US Patents, China's latest patents, Technical Efficacy Thesaurus, Application Domain, Technology Topic, Popular Technical Reports.
© 2025 PatSnap. All rights reserved.Legal|Privacy policy|Modern Slavery Act Transparency Statement|Sitemap|About US| Contact US: help@patsnap.com