Biomass particle molding module and biomass particle molding machine
A biomass granule and granule molding technology, which is applied in the direction of material forming presses, mold extrusion granulation, presses, etc., can solve the problems that affect the production of biomass granules and the difficulty of entering biomass materials, and achieve increased extrusion Pressure and anti-slip ability, avoid slipping effect
- Summary
- Abstract
- Description
- Claims
- Application Information
AI Technical Summary
Problems solved by technology
Method used
Image
Examples
Embodiment 1
[0028] Please refer to the attached figure 1 , figure 1 It is a schematic structural diagram of the biomass particle forming module provided in Embodiment 1 of the present invention.
[0029] The biomass particle molding module provided in this embodiment includes a ring die 11 and a pressing roller 12, wherein the ring die 11 is provided with a particle forming hole 112, and the pressing surface of the ring die is provided with ring die meshing teeth 111, and the pressing roller 12 The pressing surface of the ring die meshing teeth 111 is provided with a pressure roller meshing tooth 121, and the particle forming hole 112 is located between two adjacent ring die meshing teeth 111, wherein: the ring die meshing tooth 111 is set on the ring On the inner wall of the mold 11, the pressure roller 12 is located inside the ring mold 11, and the engagement teeth 111 of the ring mold and the engagement teeth 121 of the pressure roller are engaged in an inscribed engagement.
[0030]...
Embodiment 2
[0034] Please refer to the attached figure 2 , figure 2 It is a schematic structural diagram of the biomass particle forming module provided by the second embodiment of the present invention.
[0035] The biomass particle forming module provided in this embodiment includes a ring die 21 and a pressure roller, wherein the ring die 21 is provided with a particle forming hole 212, and the pressing surface of the ring die 21 is provided with a ring die meshing tooth 211, and the pressure roller On the pressing surface, there are pressure roller meshing teeth that mesh with the ring die meshing teeth 211, and the particle forming hole 212 is located between two adjacent ring die meshing teeth 211, wherein: the ring die meshing teeth 211 are set on the ring die 21 On the outer wall of the ring die 21, the pressing roller is located outside the ring die 21, and the ring die meshing teeth 211 and the pressing roller meshing teeth are circumscribed and meshed.
[0036] The working ...
Embodiment 3
[0040] Please refer to the attached Figure 3-4 , image 3 Schematic diagram of the structure of the biomass particle forming module provided by Embodiment 3 of the present invention; Figure 4 for image 3 Schematic diagram of the top view structure.
[0041] The biomass particle molding module provided in this embodiment includes a ring die 31 and a pressing roller 32, wherein the ring die 31 is provided with a particle forming hole 312, and the pressing surface of the ring die 31 is provided with ring die meshing teeth 311, and the pressing roller 32 is provided with a pressure roller meshing tooth 321 that meshes with the ring die meshing tooth 311, and the particle forming hole 312 is located between two adjacent ring die meshing teeth 311, wherein: the ring die meshing tooth 311 is arranged on On the outer wall of the ring die 31, the pressure roller 32 is located outside the ring die 31, and the engagement of the ring die meshing teeth 311 and the pressure roller mes...
PUM
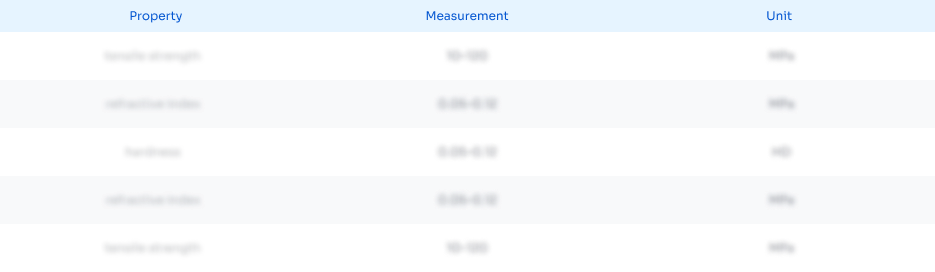
Abstract
Description
Claims
Application Information

- Generate Ideas
- Intellectual Property
- Life Sciences
- Materials
- Tech Scout
- Unparalleled Data Quality
- Higher Quality Content
- 60% Fewer Hallucinations
Browse by: Latest US Patents, China's latest patents, Technical Efficacy Thesaurus, Application Domain, Technology Topic, Popular Technical Reports.
© 2025 PatSnap. All rights reserved.Legal|Privacy policy|Modern Slavery Act Transparency Statement|Sitemap|About US| Contact US: help@patsnap.com