Preparation method of graphite heat radiation fin
A technology of graphite heat sink and manufacturing method, which is applied in the direction of electrical components, circuits, semiconductor devices, etc., can solve the problems of many impurities in products, and achieve the effects of improved mechanical strength and purity, short service life and long service life
- Summary
- Abstract
- Description
- Claims
- Application Information
AI Technical Summary
Problems solved by technology
Method used
Examples
Embodiment 1
[0017] A kind of manufacturing method of graphite heat sink described in embodiment 1 of the present invention, the manufacturing steps of graphite heat sink are:
[0018] ①Put the finely ground graphite powder with a carbon content of more than 99.999% into a strong acid and mix it with the acid treatment, and then soak it at a temperature above 100°C for 150 minutes;
[0019] ②Wash the acid-treated graphite powder to a pH value of 6.6-6.8;
[0020] ③Then add graphite powder and metal powder, silane coupling agent, and titanate coupling agent into pure water and mix thoroughly, expand the mixture at a high temperature of 1000°C-1200°C for 2 hours, and then slowly cool to room temperature Carry out drying, obtain graphite compound;
[0021] ④ Extrude the graphite compound into a sheet-shaped graphite heat sink through the graphite coil equipment;
[0022] ⑤ spray aluminum on the surface of the graphite heat sink.
[0023] The mass percentage of each component in the mixture...
PUM
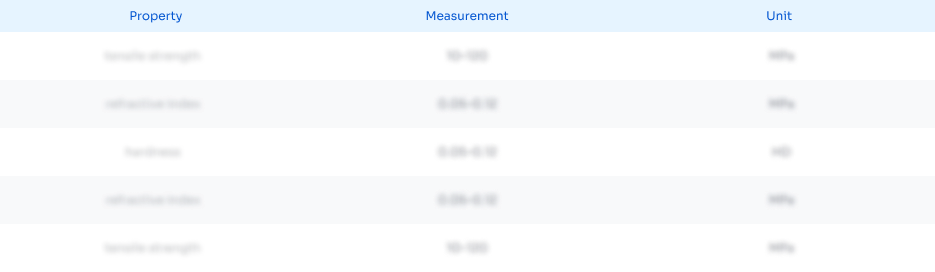
Abstract
Description
Claims
Application Information

- R&D
- Intellectual Property
- Life Sciences
- Materials
- Tech Scout
- Unparalleled Data Quality
- Higher Quality Content
- 60% Fewer Hallucinations
Browse by: Latest US Patents, China's latest patents, Technical Efficacy Thesaurus, Application Domain, Technology Topic, Popular Technical Reports.
© 2025 PatSnap. All rights reserved.Legal|Privacy policy|Modern Slavery Act Transparency Statement|Sitemap|About US| Contact US: help@patsnap.com