Heat process capable of lowering ductile-brittle transition temperature and intergranular fracture ratio of turbine blades
A technology of ductile-brittle transition temperature and intergranular fracture, applied in heat treatment furnaces, heat treatment equipment, heat treatment process control, etc., can solve the problem of high ductile-brittle transition temperature and intergranular fracture ratio of high-temperature residence time blades, and reduce the ductility and brittleness of turbine blades. The transition temperature, intergranular fracture ratio, and process effects are easily affected by the chemical composition of the blade raw materials, etc.
- Summary
- Abstract
- Description
- Claims
- Application Information
AI Technical Summary
Problems solved by technology
Method used
Image
Examples
Embodiment 1
[0008] (1) Select X20Cr13 material blades, put the blades evenly into the general quenching material basket according to the process plan, and then put the quenching material basket into the heat treatment quenching furnace;
[0009] (2) The first quenching: the quenching temperature is 980 °C, the temperature is kept for 3 hours, the cooling rate is 30 °C / min, and the quenching cooling medium is air;
[0010] (3) The second quenching: the quenching temperature is 960°C, the heat preservation is 100 minutes, the cooling rate is 40°C / min, and the quenching cooling medium is oil;
[0011] Compared with the conventional process, the ductile-brittle transition temperature (FATT) of the blade processed by the above heat treatment process 50 ) and the intergranular fracture ratio are shown in Table 1.
[0012]
Embodiment 2
[0014] (1) Select X20Cr13 material blades, put the blades evenly into the general quenching material basket according to the process plan, and then put the quenching material basket into the heat treatment quenching furnace;
[0015] (2) The first quenching: the quenching temperature is 1020°C, the temperature is kept for 2 hours, the cooling rate is 50°C / min, and the quenching cooling medium is water;
[0016] (3) The second quenching: the quenching temperature is 980°C, the temperature is kept for 15 minutes, the cooling rate is 40°C / min, and the quenching cooling medium is oil;
[0017] Compared with the conventional process, the ductile-brittle transition temperature (FATT) of the blade processed by the above heat treatment process 50 ) and the intergranular fracture ratio are shown in Table 2.
[0018]
Embodiment 3
[0020] (1) Select X20Cr13 material blades, put the blades evenly into the general quenching material basket according to the process plan, and then put the quenching material basket into the heat treatment quenching furnace;
[0021] (2) The first quenching: the quenching temperature is 1030°C, the temperature is kept for 1 hour, the cooling rate is 30°C / min, and the quenching cooling medium is air;
[0022] (3) The second quenching: the quenching temperature is 950°C, the temperature is kept for 30 minutes, the cooling rate is 50°C / min, and the quenching cooling medium is water;
[0023] Compared with the conventional process, the ductile-brittle transition temperature (FATT) of the blade processed by the above heat treatment process 50 ) and the intergranular fracture ratio are shown in Table 3.
[0024]
PUM
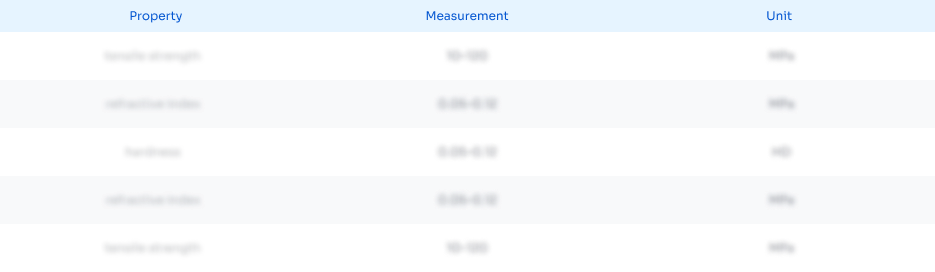
Abstract
Description
Claims
Application Information

- R&D
- Intellectual Property
- Life Sciences
- Materials
- Tech Scout
- Unparalleled Data Quality
- Higher Quality Content
- 60% Fewer Hallucinations
Browse by: Latest US Patents, China's latest patents, Technical Efficacy Thesaurus, Application Domain, Technology Topic, Popular Technical Reports.
© 2025 PatSnap. All rights reserved.Legal|Privacy policy|Modern Slavery Act Transparency Statement|Sitemap|About US| Contact US: help@patsnap.com