Polyester fiber finishing material and preparation method thereof
A polyester fiber and integer technology, which is applied in the field of polyester fiber finishing materials and its preparation, can solve the problems of lack of lasting antistatic and moisture absorption and perspiration functions and single functions, and achieves enhanced moisture absorption and perspiration functions and good softness. , smooth effect
- Summary
- Abstract
- Description
- Claims
- Application Information
AI Technical Summary
Problems solved by technology
Method used
Image
Examples
Embodiment 1
[0051] 1), 0.02 moles (n=150, molecular weight about 7350) of allyl polyether (R 1 = H and R 1 =CH 3 The ratio of 10:5, that is, -CH in allyl polyether 2 CH 2 O-Link and -CH 2 CH(CH 3 ) into the reaction flask, at 25°C, add 0.01 mole of hydrogen-terminated silicone oil (z=1, x=62, molecular weight about 5000) with the structure shown in formula III, and stir evenly. Heat up to 110°C, start to drop an appropriate amount of isopropanol solution of chloroplatinic acid, so that the concentration of chloroplatinic acid in the system is 30 ppm by weight, and keep the reaction for 5 hours. Sampling was carried out by infrared spectroscopy to determine that the H peak at 2222-2128 cm-1 disappeared, and the reaction was terminated. After cooling to below 40°C, the polyether silicone copolymer with the structure shown in formula IV is obtained, and the appearance is light yellow oily liquid.
[0052] 2), 0.01 moles of polyether (m=41, molecular weight about 2000, R 3 = H and R ...
Embodiment 2
[0055] 1), 0.02 moles (n=30, molecular weight about 1520) of allyl polyether (R 1 = H and R 1 =CH 3 The ratio of 10:5) was added to the reaction flask, and 0.01 mole of hydrogen-terminated silicone oil (z=10, x=29, molecular weight about 6000) with the structure shown in formula III was added at 25°C, and stirred evenly. Heat up to 100°C, start to drop an appropriate amount of isopropanol solution of chloroplatinic acid, so that the concentration of chloroplatinic acid in the system is 50 ppm by weight, and keep the reaction for 5 hours. The H peak at 2222-2128 cm-1 as measured by infrared spectroscopy disappeared, and the reaction was terminated. After cooling to below 40°C, the polyether silicone copolymer with the structure shown in formula IV is obtained, and the appearance is light yellow oily liquid.
[0056] 2), replace dimethyl terephthalate with 0.02 mole of dimethyl terephthalate monosulfonic acid sodium salt, and add 0.5 mmol of tetrabutyl titanate, and the rest ...
Embodiment 3
[0059] 1), 0.02 moles (n=100, molecular weight about 4900) of allyl polyether (R 1 = H and R 1 =CH 3 ratio of 10:5) into the reaction flask, at 25°C, add 0.01 mole of hydrogen-terminated silicone oil (z=15, x=11, molecular weight is about 6500) with the structure shown in formula III, stir evenly, and heat up to 150°C , start to drop an appropriate amount of chloroplatinic acid isopropanol solution, so that the weight percentage concentration of chloroplatinic acid in the system is 50ppm, and keep the reaction for 5 hours. The H peak at 2222-2128 cm-1 as determined by infrared spectroscopy disappeared, and the reaction was terminated. After cooling to below 40°C, the polyether silicone copolymer with the structure shown in formula IV is obtained, and the appearance is light yellow oily liquid.
[0060] 2), 0.01 moles of polyether (m=82, molecular weight about 4000, R 3 = H and R 3 =CH 3 The ratio of 10:5) was added to the reaction flask with a fractionation device, and t...
PUM
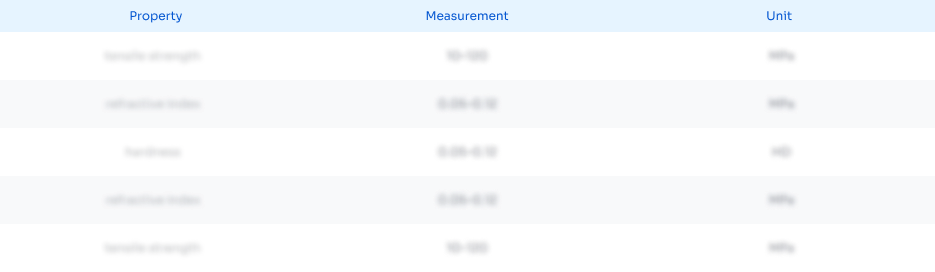
Abstract
Description
Claims
Application Information

- Generate Ideas
- Intellectual Property
- Life Sciences
- Materials
- Tech Scout
- Unparalleled Data Quality
- Higher Quality Content
- 60% Fewer Hallucinations
Browse by: Latest US Patents, China's latest patents, Technical Efficacy Thesaurus, Application Domain, Technology Topic, Popular Technical Reports.
© 2025 PatSnap. All rights reserved.Legal|Privacy policy|Modern Slavery Act Transparency Statement|Sitemap|About US| Contact US: help@patsnap.com