Method for preparing chitosan fibers
A chitosan fiber, chitosan technology, applied in spinning solution preparation, fiber chemical characteristics, wet spinning, etc., can solve the problems of poor mechanical properties of chitosan fiber, reduced molecular weight of chitosan, polydispersity, etc. , to achieve the effect of favoring orientation alignment, improving mechanical properties, and ensuring non-hydrolysis
- Summary
- Abstract
- Description
- Claims
- Application Information
AI Technical Summary
Problems solved by technology
Method used
Examples
Embodiment 1
[0013] 1) Take each component according to the weight percentage content: 9.0g chitosan, 12.0g lithium hydroxide, 1.5g sodium hydroxide, 18.0g urea, 0.3g glycerol, and the rest are water, a total of 300g; Swell for 3 hours after mixing, freeze the swelling solution at -60°C for 1 hour, and then thaw at room temperature to obtain a chitosan solution;
[0014] 2) The chitosan solution is filtered and degassed by a centrifuge to obtain a chitosan spinning solution;
[0015] 3) The chitosan spinning solution is injected into a coagulation bath with a temperature of 30 ° C to form fibers, and the coagulation bath used is 18.0% H 2 SO 4 , to obtain chitosan fibrils;
[0016] 4) After the chitosan primary fiber was washed with water at 25°C, it was air-dried at 20°C. White chitosan fibers were obtained.
Embodiment 2
[0018] 1) Take each component according to the weight percentage content: 9.0g chitosan, 15.0g lithium hydroxide, 3.0g sodium hydroxide, 18.0g urea, 1.5g glycerol, and the rest are water, a total of 300g; Swell for 3 hours after mixing, freeze the swelling solution at -40°C for 2 hours, and then thaw at room temperature to obtain a chitosan solution;
[0019] 2) The chitosan solution is filtered and degassed by a centrifuge to obtain a chitosan spinning solution;
[0020] 3) The chitosan spinning solution is injected into a coagulation bath with a temperature of 30 ° C to form fibers, and the coagulation bath used is H with a mass fraction of 10.0 % 2 SO 4 and ethanol in a volume ratio of 2:7 to obtain chitosan protofibers;
[0021] 4) After washing the primary chitosan fibers at 5°C, they were dried at 50°C to obtain white chitosan fibers.
Embodiment 3
[0023] 1) Take each component according to the weight percentage content: 9.0g chitosan, 15.0g lithium hydroxide, 1.5g sodium hydroxide, 21.0g urea, 1.5g glycerol, and the rest are water, a total of 300g; Swell for 3 hours after mixing, freeze the swelling solution at -30°C for 3 hours, and then thaw at room temperature to obtain a chitosan solution;
[0024] 2) The chitosan solution is filtered and degassed by a centrifuge to obtain a chitosan spinning solution;
[0025] 3) The chitosan spinning solution was injected into a coagulation bath with a temperature of 30 ° C to form fibers, and the coagulation bath used was 8.0% H 2 SO 4 , ethanol and mass fraction are 5.0% NaCl by volume ratio 3:6:1 mixed solution, obtain chitosan protofiber;
[0026] 4) Washing the primary chitosan fibers with water at 10°C and drying at 30°C to obtain white chitosan fibers.
PUM
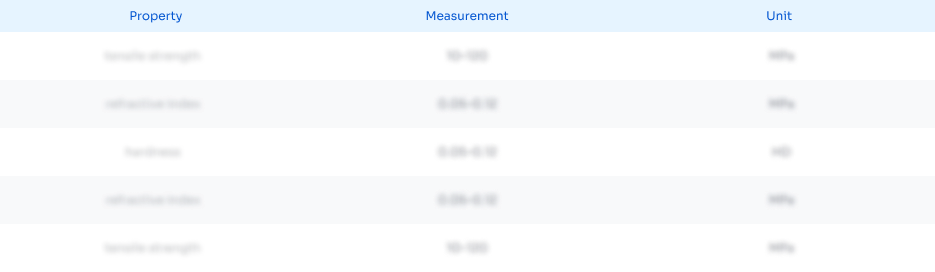
Abstract
Description
Claims
Application Information

- R&D
- Intellectual Property
- Life Sciences
- Materials
- Tech Scout
- Unparalleled Data Quality
- Higher Quality Content
- 60% Fewer Hallucinations
Browse by: Latest US Patents, China's latest patents, Technical Efficacy Thesaurus, Application Domain, Technology Topic, Popular Technical Reports.
© 2025 PatSnap. All rights reserved.Legal|Privacy policy|Modern Slavery Act Transparency Statement|Sitemap|About US| Contact US: help@patsnap.com