Method of preparing propylene by oxygen-containing compounds
A compound and propylene technology, which is applied in the direction of producing hydrocarbons, hydrocarbons, hydrocarbons, etc. from oxygen-containing organic compounds, can solve problems that do not involve improving the selectivity of oxygen-containing compounds to propylene, and achieve suppression of side reactions and improvement of acid strength , improve the effect of selectivity
- Summary
- Abstract
- Description
- Claims
- Application Information
AI Technical Summary
Problems solved by technology
Method used
Image
Examples
preparation example Construction
[0052] The preparation of catalyst used in the embodiment: in 175 kilograms of aluminum sols (Sinopec Catalyst Qilu Branch Company product, containing Al 2 o 3 11.4% by weight, the pH value is 2~3), add 62.5 kilograms of kaolin (the industrial product of Suzhou porcelain clay company, solid content 80 weight %), add 100 kilograms of Fe-ZRP-1.5 zeolite slurry (solid content is 30 weight %) and 162.5 kg of decationized water, homogenized, spray-dried, washed with deionized water until the pH value was 6, dried, and calcined at 500°C for 3 hours to obtain catalyst sample A, correspondingly prepared Mg-ZRP-1.5-containing Catalyst B, Catalyst C containing Ni-ZRP-1.5.
[0053] The fresh catalysts are subjected to water vapor aging pretreatment before use, and the aging pretreatment conditions are: 790°C, 100% water vapor atmosphere, and the aging time is 14h.
[0054] The oxygen-containing compound used in the experiment is methanol (product of Beijing Chemical Plant), its properti...
Embodiment 1
[0062] Adopt catalyst A, methanol enters riser reactor 1, contacts with the spent catalyst (coke content is 1% by weight) from stripper and the heat regenerated catalyst from regenerator, and the spent catalyst and regenerated catalyst weight ratio are 70 : 30. The reacted reactant flow and the reacted catalyst are separated in the settler, the reactant flow is introduced into the product separation system, and the separated catalyst enters the reactor 3 . The raw material containing 5% by weight of ethylene and 95% by weight of light olefin materials (see Table 2 for properties) is introduced into the riser reactor 2, and reacts with the hot regenerated catalyst from the regenerator. The reactant stream and the catalyst are not separated and directly enter the reaction Reactor 3 further reacts; the reactant stream leaving reactor 3 is introduced into settler 5, and then introduced into the product separation system, the catalyst leaving reactor 3 is introduced into stripper, ...
Embodiment 2
[0064] Using catalyst A, methanol enters riser reactor 1 and the contact reaction of the spent catalyst (coke content 1% by weight) from the stripper and the hot catalyst from the regenerator, and the spent catalyst and regenerated catalyst weight ratio is 75:25 , after the reaction, the reactant flow comprising propylene is separated from the reacted catalyst and introduced into the product separation system, the separated catalyst is introduced into the reactor 3, and introduced into the stripper for stripping through the reactor 3; the light olefin material described in Table 2 At a reaction temperature of 40°C, a reaction pressure of 0.5 MPa, and a mol ratio of hydrogen to olefins of 4:1, on catalyst RDD-1 (product of Sinopec Catalyst Changling Branch), through selective hydrogenation reaction, diolefins and alkynes After hydrocarbons are converted into olefins, they are introduced into riser reactor 2, and ethylene, which accounts for 10% of the total weight of ethylene an...
PUM
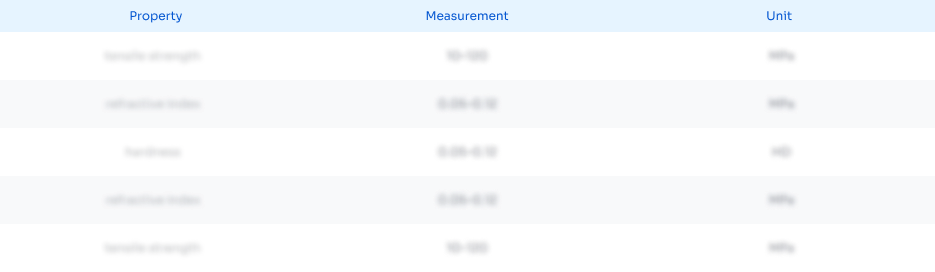
Abstract
Description
Claims
Application Information

- R&D Engineer
- R&D Manager
- IP Professional
- Industry Leading Data Capabilities
- Powerful AI technology
- Patent DNA Extraction
Browse by: Latest US Patents, China's latest patents, Technical Efficacy Thesaurus, Application Domain, Technology Topic, Popular Technical Reports.
© 2024 PatSnap. All rights reserved.Legal|Privacy policy|Modern Slavery Act Transparency Statement|Sitemap|About US| Contact US: help@patsnap.com