Multidirectional extrusion molding process and die for aluminum alloy shell parts with branches
A multi-directional extrusion and forming die technology, applied in metal extrusion dies and other directions, to achieve the effects of uniform strain, high production efficiency, and convenient and simple operation
- Summary
- Abstract
- Description
- Claims
- Application Information
AI Technical Summary
Problems solved by technology
Method used
Image
Examples
Embodiment Construction
[0023] In this example, the Figure 1-A with Figure 1-B The single-part drawings shown in are for object specific description. The part 1 is an aluminum alloy hollow shell with a branch-like part 2 at the bottom.
[0024] The present invention will process the mold that part 1 adopts such as figure 2 As shown, it mainly includes vertical punch 3, upper connecting template 4, active radial outer mold sleeve 5, left split die 6, right split die 7, right connecting head 8, left connecting head 9, right connecting rod 10, left connecting rod 11, right horizontal connecting template 12, left horizontal connecting template 13, guide rail seat plate 14.
[0025] The vertical punch 3 is independently connected and driven by the punching cylinder of the multi-directional forming hydraulic press to move vertically up and down. The vertical punch 3 is positioned above the left split die 6 and the right split die 7, and is aligned at the opening of the die cavity. The upper connect...
PUM
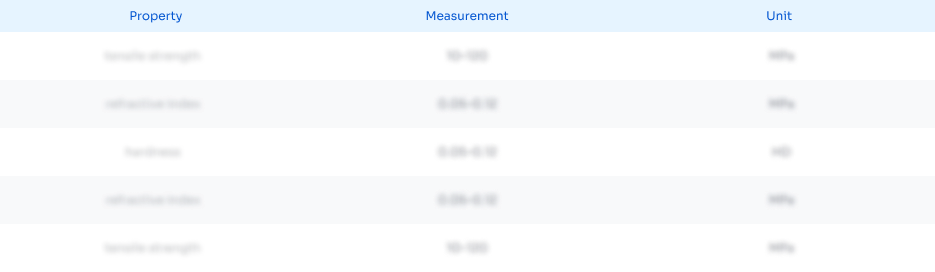
Abstract
Description
Claims
Application Information

- R&D
- Intellectual Property
- Life Sciences
- Materials
- Tech Scout
- Unparalleled Data Quality
- Higher Quality Content
- 60% Fewer Hallucinations
Browse by: Latest US Patents, China's latest patents, Technical Efficacy Thesaurus, Application Domain, Technology Topic, Popular Technical Reports.
© 2025 PatSnap. All rights reserved.Legal|Privacy policy|Modern Slavery Act Transparency Statement|Sitemap|About US| Contact US: help@patsnap.com