Process for synthesizing o-cresol formaldehyde epoxy resin with low chlorine content
A phenolic epoxy resin, a synthesis process technology, applied in other chemical processes, chemical instruments and methods, etc., can solve the problems of hindering the addition of phenolic group and epichlorohydrin etherification reaction, easy deepening of color, complicated operation, etc. To achieve the effect of controllable reaction process conditions, increase epoxy value and reduce chlorine content
- Summary
- Abstract
- Description
- Claims
- Application Information
AI Technical Summary
Benefits of technology
Problems solved by technology
Method used
Examples
Embodiment 1
[0019] Example 1: Carry out the first step, add 225g of o-cresol and 962g of epichlorohydrin into a four-neck flask with stirring and a thermometer, heat with nitrogen, add 183.3g of NaOH with a mass fraction of 50%, and heat at 60°C After reacting for 4 hours, proceed to step 2, recover epichlorohydrin under reduced pressure, wash with water until neutral, and obtain chlorohydrin ether monomer. At this time, based on the calculated theoretical value of the chlorohydrin ether monomer, the amount of formaldehyde that should be added is obtained. After the chlorohydrin ether monomer is obtained, the third step can be carried out. To the obtained chlorohydrin ether monomer, 139g of formaldehyde solution with a mass fraction of 36% is added, the temperature is raised to 100°C, 15g of hypophosphorous acid is added in portions, and as a metal assistant Add 3g of zinc powder as an additive, react for 8h, then proceed to the fourth step, need to add 200g of toluene and 200g of n-butan...
Embodiment 2
[0021] Carry out the first step, add 225g of o-cresol and 1154g of epichlorohydrin into a four-neck flask with a stirring and thermometer, heat with nitrogen, add 330g of NaOH with a mass fraction concentration of 50%, and react at 70°C for 6 hours. Go to step 2, recover epichlorohydrin under reduced pressure, wash with water 3 times until neutral, and obtain chlorohydrin ether monomer. At this time, based on the calculated theoretical value of the chlorohydrin ether monomer, the amount of formaldehyde that should be added is obtained. After the chlorohydrin ether monomer is obtained, the third step can be carried out. Add 139 g of formaldehyde solution with a mass fraction concentration of 36% to the obtained chlorohydrin ether monomer, raise the temperature to 95° C., add 28 g of hypophosphorous acid in stages, and add Add 3g of zinc powder, react for 10h, then proceed to the fourth step, need to add 200g of toluene and 200g of n-butanol to dissolve, add 50g of NaOH with a m...
Embodiment 3
[0023] Carry out the first step, add 225g of o-cresol and 770g of epichlorohydrin into a four-neck flask with stirring and a thermometer, heat with nitrogen gas, add 183g of NaOH with a mass fraction concentration of 60%, and react at 80°C for 2 hours. Go to step 2, recover epichlorohydrin under reduced pressure, wash with water 3 times until neutral, and obtain chlorohydrin ether monomer. At this time, based on the calculated theoretical value of the chlorohydrin ether monomer, the amount of formaldehyde that should be added is obtained. After the chlorohydrin ether monomer is obtained, the third step can be carried out. To the obtained chlorohydrin ether monomer, 139 g of formaldehyde solution with a mass fraction concentration of 36% is added, the temperature is raised to 105° C., and 40 g of hydrochloric acid with a mass fraction concentration of 20% is added in portions. , add 4g of zinc powder as a metal additive, react for 4h, then proceed to the fourth step, need to ad...
PUM
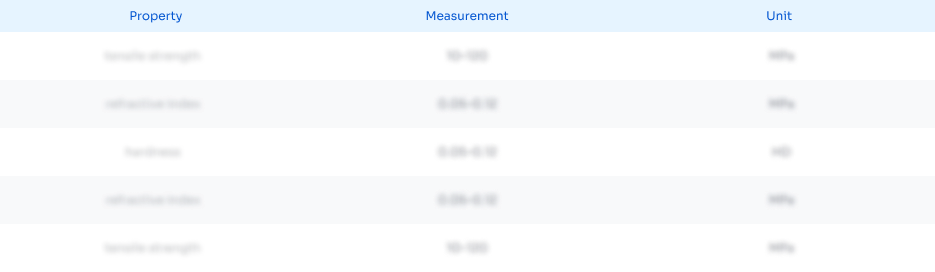
Abstract
Description
Claims
Application Information

- R&D Engineer
- R&D Manager
- IP Professional
- Industry Leading Data Capabilities
- Powerful AI technology
- Patent DNA Extraction
Browse by: Latest US Patents, China's latest patents, Technical Efficacy Thesaurus, Application Domain, Technology Topic, Popular Technical Reports.
© 2024 PatSnap. All rights reserved.Legal|Privacy policy|Modern Slavery Act Transparency Statement|Sitemap|About US| Contact US: help@patsnap.com