Method for preparing packaging material
A packaging and formulation technology, applied in textiles, papermaking, fiber raw material processing, etc., can solve the problems of increased processing costs, damage, and environmental pollution, and achieve the effect of improving efficiency and speed, and simple process
- Summary
- Abstract
- Description
- Claims
- Application Information
AI Technical Summary
Problems solved by technology
Method used
Examples
Embodiment 1
[0042] Example 1. Preparation of packaging paper products using rice straw
[0043] For 100 kg of rice straw, the multi-enzyme compound preparation used in this example is prepared by adding 35-70 kg of water to 0.7 kg of the multi-enzyme compound, and the multi-enzyme compound includes the following components by weight: 31- 33 parts of laccase; 25-26 parts of xylanase; 10-15 parts of pectinase; 1-5 parts of amylase; 6-8 parts of lipase; 3-5 parts of tannase; 1-3 parts of coenzyme; 2-3 parts of stabilizer; 3-5 parts of diatomaceous earth; diatomaceous earth; said stabilizer is composed of stabilizer A, stabilizer B and stabilizer C; said stabilizer Agent A accounts for 30% of the amount of stabilizer formula, by Ca 2+ and polyvinylpyrrolidone; the stabilizer B accounts for 50% of the stabilizer formula, consisting of EDTA and dithiothreitol; the stabilizer C accounts for 20% of the stabilizer formula, composed of polyvinylpyrrolidone and EDTA composition. Wherein said stab...
Embodiment 2
[0059] Embodiment 2, utilize corn stalk to carry out the processing of meal box
[0060] For 100 kg of corn stalks, the multi-enzyme compound preparation used in this example is prepared by adding 45-65 kg of water to 1 kg of the multi-enzyme compound, and the multi-enzyme compound includes the following components by weight: 30-31 27-28 parts of xylanase; 15-20 parts of pectinase; 3-5 parts of amylase; 0.5-3 parts of lipase; 0.1-1 part of tannase; 0.5 -1 part of coenzyme; 1-3 parts of stabilizer; 10-15 parts of diatomaceous earth; the stabilizer is composed of stabilizer A, stabilizer B and stabilizer C; the stabilizer A accounts for the stabilizer formula 30% of the amount consists of Ca 2+ and polyvinylpyrrolidone; the stabilizer B accounts for 50% of the stabilizer formula, consisting of EDTA and dithiothreitol; the stabilizer C accounts for 20% of the stabilizer formula, composed of polyvinylpyrrolidone and EDTA Composition; Ca in the stabilizer A 2+ The weight ratio w...
Embodiment 3
[0078] Embodiment 3, utilize wheat straw to carry out the processing of agricultural product packing box
[0079] For 100 kg of wheat straw, the multi-enzyme compound preparation used in this example is prepared from 0.85 kg of multi-enzyme compound plus 43-50 kg of water, and the multi-enzyme compound includes the following components by weight: 33 parts laccase; 25-26 parts of xylanase; 10-11 parts of pectinase; 1-3 parts of amylase; 8-9 parts of lipase; 3-5 parts of tannase; 0.1- 1 part of coenzyme; 1-3 parts of stabilizer; 3-10 parts of diatomaceous earth; the stabilizer is composed of stabilizer A, stabilizer B and stabilizer C; the stabilizer A accounts for the amount of stabilizer formula 30% of Ca 2+ and polyvinylpyrrolidone; the stabilizer B accounts for 50% of the stabilizer formula, consisting of EDTA and dithiothreitol; the stabilizer C accounts for 20% of the stabilizer formula, composed of polyvinylpyrrolidone and EDTA Composition; Ca in the stabilizer A 2+ Th...
PUM
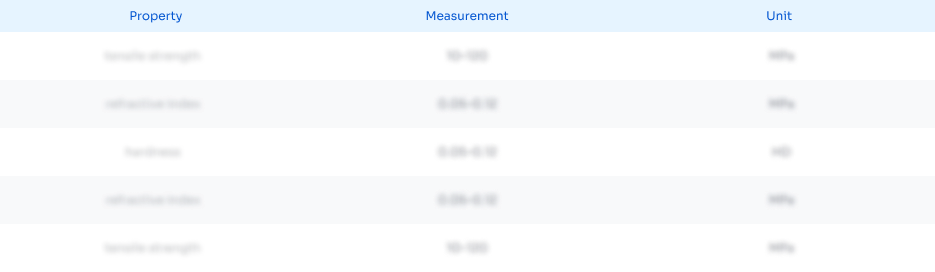
Abstract
Description
Claims
Application Information

- R&D Engineer
- R&D Manager
- IP Professional
- Industry Leading Data Capabilities
- Powerful AI technology
- Patent DNA Extraction
Browse by: Latest US Patents, China's latest patents, Technical Efficacy Thesaurus, Application Domain, Technology Topic, Popular Technical Reports.
© 2024 PatSnap. All rights reserved.Legal|Privacy policy|Modern Slavery Act Transparency Statement|Sitemap|About US| Contact US: help@patsnap.com