Ultrasonic auxiliary micro injection forming die
A molding mold and ultrasonic technology, applied in the field of polymer ultrasonic-assisted micro-injection molding molds, can solve problems such as uneven heat loss, narrow processing temperature range, high material melting temperature and mold temperature, and improve fluidity and filling performance, improved injection molding quality, viscosity and elastic reduction effects
- Summary
- Abstract
- Description
- Claims
- Application Information
AI Technical Summary
Problems solved by technology
Method used
Image
Examples
Embodiment Construction
[0013] Below in conjunction with specific embodiment, and with reference to accompanying drawing, technology of the present invention is described further:
[0014] A kind of ultrasonic-assisted micro-injection molding mold as shown in the figure, it comprises static mold 9 and moving mold 7, described static mold 9 comprises static mold fixed plate 19, is connected with static mold on described static mold fixed plate 19 The template 14 is fixedly connected with the static mold insert 18 on which the static mold core 16, the sprue bushing 10 and the static mold runner 17 are fixedly connected in the middle of the static mold template 14; the movable mold 7 Including the movable mold template 20 fixedly connected with the movable mold insert 21 in the middle, the movable mold fixed plate 26 is fixedly connected with the movable mold template 20 arranged above it through the baffle plate 25 (can be a square iron), and the baffle plate 25 is connected with the movable mold templa...
PUM
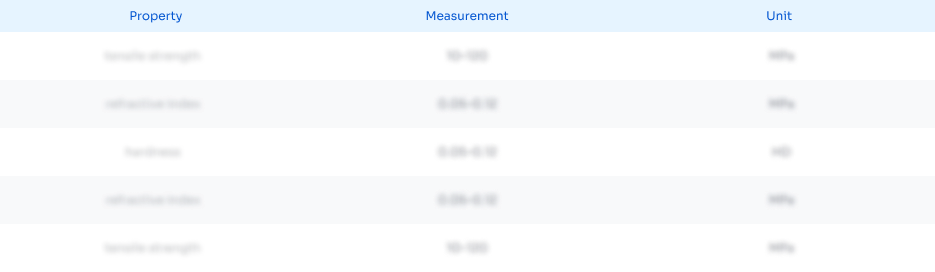
Abstract
Description
Claims
Application Information

- R&D
- Intellectual Property
- Life Sciences
- Materials
- Tech Scout
- Unparalleled Data Quality
- Higher Quality Content
- 60% Fewer Hallucinations
Browse by: Latest US Patents, China's latest patents, Technical Efficacy Thesaurus, Application Domain, Technology Topic, Popular Technical Reports.
© 2025 PatSnap. All rights reserved.Legal|Privacy policy|Modern Slavery Act Transparency Statement|Sitemap|About US| Contact US: help@patsnap.com