Non-woven fabric for automotive interior skin material and preparation thereof
A non-woven fabric, automotive interior technology, used in textiles and papermaking, textile decoration, fabric surface trimming, etc. The effect of elongation
- Summary
- Abstract
- Description
- Claims
- Application Information
AI Technical Summary
Problems solved by technology
Method used
Image
Examples
Embodiment approach 1
[0068] Embodiment 1: Coating method
[0069] The method of chemical coating (or adhesive coating) of the present invention is shown in Figure 9 middle.
[0070] The coating device comprises a pair of rollers, and one or both surfaces of the nonwoven may be coated by at least one coating device. If the nonwoven fabric passes between the pair of rollers rotating in opposite directions based on the central axis, an adhesive is added to one of the rollers and the surface where the nonwoven fabric adjoins each other, so that the surface of the nonwoven fabric is coated with the adhesive. the surface. ACRYSOL 890, Acrylic Emulsion DK-6800 DK Chem or EW-100S SKI PETRESIN available from DKC were used as binder.
[0071] At this time, the surfaces of the nonwoven fabric contacting the two rolls may be the same (front surface coating), or may be different (back surface coating). In addition, double surface coating is possible if front surface coating and back surface coating are ca...
Embodiment approach 2
[0072] Embodiment 2: Printing method
[0073] The printing method using the trommel method uses a printing unit in which the trommel contacts a guide roller ( Figure 10 ). With the non-woven fabric in the first color printing unit's gondola roll ( Figure 10 a) and guide roller ( Figure 10 Pass between b) in the extrusion rod ( Figure 10 d) Extrusion in the trommel through the binder supplier installed in the trommel ( Figure 10 c) Empty color binder ( Figure 10 In e), so that a part thereof is discharged from the outer surface of the trommel, thereby forming a pattern on the surface of the nonwoven fabric. Because the extrusion rod is arranged in the magnet (electromagnet) ( Figure 10 Within the range of the magnetic field of f) in, so a predetermined amount of color binder is discharged to the outside of the rotary screen by the extrusion rod at a predetermined position, thereby allowing printing. At this time, the resolution of the printed matter pattern can be...
Embodiment approach 3
[0078] Embodiment 3: Alkaline etching method
[0079] An alkaline etching method was performed on the surface of a nonwoven fabric formed of 100 wt% polyester. The alkaline etching method is performed by adding NaOH, a strong alkaline material, on the surface of the fiber to melt the fiber in a regular shape and depth. After printing the surface of the nonwoven fabric with an alkaline material, the printing solution and the melted portion of the nonwoven fabric are separated.
PUM
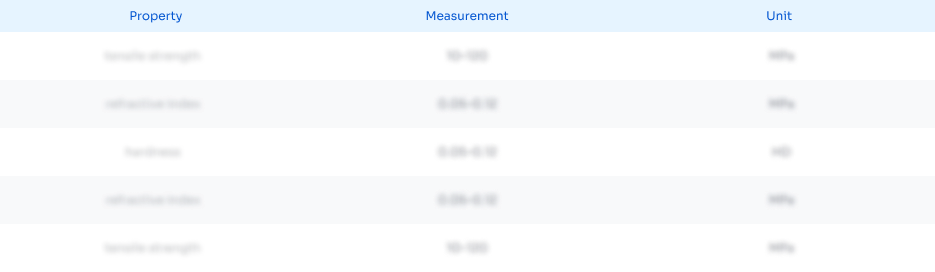
Abstract
Description
Claims
Application Information

- R&D
- Intellectual Property
- Life Sciences
- Materials
- Tech Scout
- Unparalleled Data Quality
- Higher Quality Content
- 60% Fewer Hallucinations
Browse by: Latest US Patents, China's latest patents, Technical Efficacy Thesaurus, Application Domain, Technology Topic, Popular Technical Reports.
© 2025 PatSnap. All rights reserved.Legal|Privacy policy|Modern Slavery Act Transparency Statement|Sitemap|About US| Contact US: help@patsnap.com