Friction welding method for automobile coatrack
A friction welding and coat hanger technology, applied in the field of automobile coat hanger welding and automobile coat hanger friction welding, can solve the problem of uneven distribution of welding strength, and achieve the advantages of avoiding uneven welding melting, improving strength and reducing welding time. Effect
- Summary
- Abstract
- Description
- Claims
- Application Information
AI Technical Summary
Problems solved by technology
Method used
Examples
Embodiment Construction
[0016] A friction welding method for an automobile coat rack, comprising the following steps:
[0017] (1) Put the coat rack substrate on the corresponding mold lower mold;
[0018] (2) Place the buckle seat on the mold upper mold fixture at the corresponding position of the part;
[0019] (3) The upper and lower molds are clamped, the upper mold vibrates and rubs against the lower mold, and cools down to complete the welding of the car coat rack.
[0020] The structure after friction welding is generally to make two thermoplastic products rub to generate heat, and the joint surface is heated and melted to form a whole. The car coat rack has a layer of non-woven fabric between the welding blocks, which hinders the friction of the two plastic products.
[0021] In order to increase the welding strength, glass fiber is added to the substrate. After welding, the PP material penetrates into the glass fiber gap, and reaches the strength requirement after cooling and solidificati...
PUM
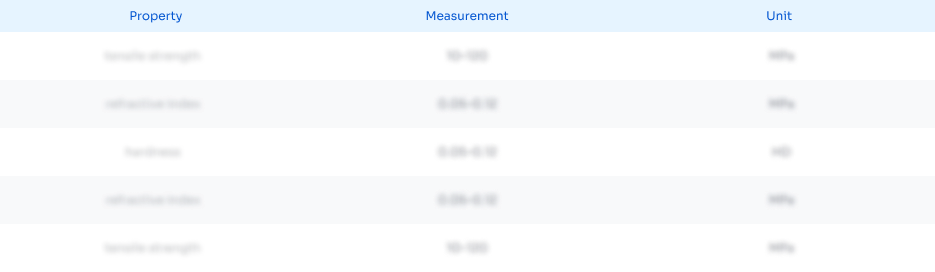
Abstract
Description
Claims
Application Information

- R&D
- Intellectual Property
- Life Sciences
- Materials
- Tech Scout
- Unparalleled Data Quality
- Higher Quality Content
- 60% Fewer Hallucinations
Browse by: Latest US Patents, China's latest patents, Technical Efficacy Thesaurus, Application Domain, Technology Topic, Popular Technical Reports.
© 2025 PatSnap. All rights reserved.Legal|Privacy policy|Modern Slavery Act Transparency Statement|Sitemap|About US| Contact US: help@patsnap.com